■ 강의 열처리 개요 강(鋼, steel)이란 기본적으로 鐵(Fe)과 2.0%이하의 炭素(C)와의 합금을 말하는 것으로, 현재 공업 및 토목건축용 재료로서 가장 널리 사용되고 있는 금속재료이다. 모든 금속재료의 생산량 중에서 강이 차지하고 있는 비율은 대략 80% 정도이다. 이와 같이 강이 널리 사용되는 이유는 염가로써 여러가지 성질을 다양하게 변화시킬 수 있고, 또 우수한 강도(强度, strength)와 함께 소성가공이 용이하므로 원하는 형상의 제품으로 제조하기가 쉽기 때문이다. 즉 자동차의 차체에 사용되는 강판은 연성이 우수하여야만 하는 반면에 절삭공구에 사용되는 강은 충분히 경화되어 내마모성이 커야만 한다. 또한 자동차의 축이나 대형선박의 프로펠러 축 등은 강도와 인성(靭性, toughness)을 겸비하여야 한다. 그리고 면도날도 극히 경도가 우수해야만 한다. 이와 같이 매우 연한 강판에서부터 극히 경한 공구강에 이르기까지 여러 가지 다양한 용도에 적합한 성질을 갖추어 주는 것은 주어진 강의 적절한 열처리에 의해서 주로 이루어지고 있다. 일반적으로 강에 열처리를 실시하는 이유는 다음 사항 중 어느 한가지 목적을 달성하기 위함이다.
① 냉간가공에 의하여 발생된 응력을 제거한다거나 또는 불균일 냉각에 의한 응력을 제거하기 위한 것이다. ② 열간가공된 강의 결정립조직을 미세화시키기 위한 것이다. ③ 바람직한 결정립조직을 유지하기 위한 것이다. ④ 경도를 감소시키고 연성을 향상시키기 위한 것이다. ⑤ 경도를 증가시켜서 내마모성을 향상시키기 위한 것이다. ⑥ 사용중 충격에 견딜 수 있도록 인성을 향상시키기 위한 것이다. ⑦ 피삭성을 향상시키기 위한 것이다. ⑧ 공구강의 절삭능력을 향상시키기 위한 것이다. ⑨ 전기적 성질을 향상시키기 위한 것이다. ⑩ 강의 자기적 성질을 개선하기 위한 것이다.
위 사항에 대한 구체적인 내용이 본 페이지의 주된 내용이 될 것이고, 여기서는 우선적으로 강의 열처리에 대하여 논하기 전에 강이란 무엇이며, 또 강의 내부구조는 어떻게 이루어져 있는지를 간단히 알아 보는 것이 도움이 되리라 생각한다. |
● 강(鋼)이란 무엇인가 ? ◆ 탄소강과 특수강 모든 강은 기본적으로 철과 탄소로 이루어진 합금이라고 부르는 것이 가장 적절하다. 일반적으로 2.0%C 이하의 철강재료를 鋼이라 하고, 2.0%C 이상의 철강재료를 주철(鑄鐵, cast iron)이라 규정하고 있으나, 1.3∼2.5%C범위의 철강재료는 실용성이 없으므로 공업적으로 거의 생산하지 않고 있다. 한편 강은 탄소강(炭素鋼, carbon steel)과 특수강(特殊鋼, special steel)으로 분류되는데, 여기서 우리는 탄소강과 특수강의 구분을 명확히 할 필요가 있다. 탄소강은 기본적으로는 Fe와 C의 2원합금이지만 일반적인 탄소강에는 C 이외에 Si, Mn, P, S 등의 불순물이 소량 함유되어 있는데, 이들 원소는 특별히 어떤 목적을 위해서 첨가된 것이 아니라 제선과정중에 광석이나 scrap으로부터 혼입되었든가 아니면 정련과정에서 첨가된 것이 잔존하는 것이기 때문에 이들 원소가 함유되어있다 할지라도 특수강이라 부르지 않는다. 한 예로 KS규격에 기계구조용 탄소강재로 규정된 SM 45C강의 공칭성분은 0.45C, 0.75Mn, 0.04P, 0.05S 및 0.22Si 이다. 한편 특수강을 정확히 정의한다는 것은 쉬운 일은 아니지만, 일반적으로는 탄소강에서는 얻을 수 없는 특수한 성질을 얻기 위하여 1종 또는 그 이상의 합금원소를 첨가시킨 강을 말한다. 그 예로서 스테인리스강은 Cr을 12%이상 첨가하여 내식성을 향상시켰고, 합금공구강은 Cr, Mo,V 등의 원소를 첨가하여 내마모성과 더불어 열처리특성을 향상시킨 특수강의 전형적인 예이다. |
◆ 탄소량에 따른 분류 대부분의 탄소강에 있어서 함유된 탄소량에 따라서 강의 성질과 적절한 열처리방법이 결정되기 때문에 가장 중요한 원소는 탄소이다. 이와같이 탄소량의 실제적인 중요성 때문에 탄소강을 분류하는 한가지 방법이 바로 이 탄소량에 따른 분류이다. 일반적으로 0.3wt% 이하의 탄소를 함유하는 탄소강을 저탄소강(低炭素鋼, low carbon steel) 또는 연강(軟鋼, mild steel)이라고 부르고, 0.3∼0.6wt%의 탄소량을 함유하는 탄소강을 중탄소강(中炭素鋼, medium-carbon steel), 그리고 0.6wt% 이상의 탄소량을 가진 탄소강을 고탄소강(高炭素鋼, high-carbon steel)이라고 한다. 고탄소강 중 0.77%C 이상의 탄소강을 특히 공구강(工具鋼, tool steel)이라고 부른다. 한편 1.3wt% 이상의 탄소를 함유하는 강은 몇가지 공구강을 제외하고는 거의 사용되지 않고 있다. |
● 강(鋼)과 열처리(熱處理) 전술한 바와 같이 강의 용도가 다양하고 그 사용량도 큰 이유는 첫째, 탄소량에 따라서 기계적성질이 현저하게 변화된다는 것이다. 표 1.1은 순철(0%C), 0.2%C강 및 0.8%C강을 서냉시킨 후의 항복강도를 나타낸 것으로서, 탄소량이 0%에서 0.8%로 증가함에 따라 항복강도가 4배 이상 증가하고 있는 것을 보여주고 있다. 
이와같이 서냉시켰을 때 탄소량이 증가함에 따라서 강도가 높아지는 이유는 시멘타이트(cementite : Fe3C)라고 불리우는 철탄화물의 양이 증가되기 때문이다. 즉 이 탄화물은 매우 硬하기 때문에 강 속에 존재하게 되면 강도 및 경도를 향상시키게 된다. 강이 널리 사용되는 또 하나의 이유는 열처리에 의해서 그 기계적성질을 매우 다양하게 변화시킬 수 있다는 것이다. 즉 다른 금속재료에 비해서 열처리효과가 매우 현저하기 때문에 그 응용범위가 확장되고 있는 것이다. 그림 1.1은 Fe-0.8%C강을 900℃로부터 냉각시킬 떄 냉각속도에 따른 항복강도의 변화를 나타낸 것으로 냉각속도가 증가됨에 따라 항복강도가 급격하게 증가된다는 사실을 알 수 있다. 즉 이 3개의 시료는 동일한 탄소량을 함유할지라도 열처리시 냉각방법에 따라서 기계적성질이 변화하고 있다. 이와같이 냉각속도에 따라 강도가 증가되는 이유는 강의 내부조직이 변화되기 때문인데, 실제로 모든 금속재료의 성질(특히 기계적성질)은 그 금속의 내부구조에 거의 직접적으로 의존하고 있다. 우리는 이 내부구조를 흔히 미세조직(微細組織, microstructure)이라고 부른다. 한편 탄소강의 경우 동일한 탄소량에서도 열처리방법에 따라서 경도가 현저하게 달라진다는 것을 나타내고 있다. 따라서 탄소량과 열처리의 조합으로서 필요한 경도 및 강도를 용이하게 얻을 수 있다는 것을 알 수 있다. 결국 열처리를 한마디로 요약하면 「필요한 성질을 얻기 위하여 금속내부의 미세조직을 변화시키는 가열 및 냉각조작」이라고 말할 수 있다. 역으로 말하면 미세조직의 변화를 수반하지 않는 가열 및 냉각과정은 기계적성질의 변화를 거의 나타내지 않으므로 열처리라고 말하기는 어렵다는 것이다.
|
● 철 및 강의 결정구조 모든 금속은 특별한 경우(비정질)를 제외하고는 고체상태에서 규칙적인 원자배열을 하고 있다. 이것이 금속의 일반적인 특징중의 하나이다. 결정이란 원자가 규칙적인 배열을 하고 있는 것을 말하며, 금속의 결정은 매우 미시적인 것이므로 육안으로는 볼 수 없고 X-선으로 조사해야만 확인할 수 있다. |
◆ 철의 결정구조 순철을 상온으로부터 가열하면서 그 체적변화를 측정하면 910℃ 및 1390℃에서 큰 변화가 일어나는 것을 볼 수 있다. 이것은 이 온도를 경계로 하여 결정격자가 갑자기 변화하기 때문으로, 910℃를 A3변태점, 1390℃를 A4변태점이라고 부른다. 순철은 A3변태점 이하의 온도에서는 체심입방격자(體心立方格子, body-centered cubic : BCC)의 형태를 나타내는데, 입방체의 각 꼭지점(8개)에 1개씩, 그리고 입방체의 중심에 1개의 원자가 존재하는 형태이다. 이것을 금속조직학에서는 α鐵(α-Fe)라고 부른다. 또한 A3변태점과 A4변태점 사이의 온도에서 순철은 면심입방격자(面心立方格子, face-centered cubic : FCC)의 형태를 나타내는데, 이 결정격자의 원자배열은 8개의 꼭지점에 각각 1개씩의 원자가 존재하는 것은 BCC와 동일하지만 체심에는 원자가 없고 입방체의 6면 중심에만 각각 1개씩의 원자가 존재한다. 이것을 γ鐵(γ-Fe)이라고 한다. 한편 A4변태점 이상 융점(1534℃)까지는 재차 BCC구조로 변하는데, 이것을 δ鐵(δ-Fe)이라고 부른다. 이와같이 동일한 물질이 어느 온도를 경계로 하여 가역적으로 결정구조를 바꾸는 변태를 동소변태(同素變態, allotropic transformation)라고 한다. |
◆ 동소변태시의 체적변화 위에서 나타낸 원자충진율의 결과로부터 알 수 있듯이 BCC결정구조를 가지는 α철이 FCC결정구조를 가지는 γ철보다 밀도가 작다. 즉 γ철이 α철보다 좀더 밀집된 원자배열을 하고 있다. 그러므로 순철을 상온으로부터 가열하면 열팽창에 의해서 체적이 팽창하다가 910℃에서 α철이 γ철로 변태하면 갑자기 체적이 수축하게 된다. 계속해서 가열하면 열팽창에 의한 체적팽창을 일으키다가 1390℃에서 재차 BCC구조인 δ철로 변태하면서 급격한 체적팽창을 일으킨다. 반대로 1390℃ 이상의 온도로부터 냉각시키면 위 과정이 역으로 나타나게 된다. 1390℃에서의 급격한 수축 및 910℃에서의 급격한 팽창을 나타낸다. 특히 910℃에서의 급격한 체적팽창은 후술하는 퀜칭열처리시 변형 및 균열 등의 문제점을 일으키는 기본원리로 작용하므로 독자들은 이 사항에 대한 특별한 이해가 필요하다. |
◆ 강의 고용체 강은 철과 탄소의 합금이므로 철의 결정격자의 틈사이에 소량의 탄소가 함유된 형태로 되어 있다. α철이나 γ철이나 모두 고체이고, 여기에 고체탄소를 함유할 수 있으므로 이러한 상태를 고용체(固溶體, solid solution)라고 부른다. 고용체에는 2종류가 있다. 하나는 용매원자인 Fe 격자 사이에 비교적 원자반경이 작은 탄소원자(용질원자)가 들어가 있는 침입형 고용체(侵入型固溶體, interstitial solid solution)이고, 또하나는 Fe 격자내에 Cr이나 Ni과 같이 거의 원자반경이 비슷한 원자가 용매원자인 철원자의 일부를 대치한 치환형 고용체(置換型固溶體, substitutional solid solution)이다. α철에 탄소가 함유된 고용체를 페라이트(ferrite), γ철에 탄소가 함유된 고용체를 오스테나이트(austenite)라고 부른다. 페라이트내에 탄소의 고용한계는 상온에서 0.008%, 723℃에서 0.02%인 반면에 오스테나이트내에 탄소의 고용한계는 723℃에서 0.8%, 1147℃에서 2.0%로서 오스테나이트 속에 고용될 수 있는 탄소량이 훨씬 많다. 탄소량이 더욱 많아져서 페라이트나 오스테나이트에 대한 고용한계를 넘어서면 Fe와 C가 일정한 원자비로서 결합된 화합물인 시멘타이트(cementite : Fe3C)가 형성된다. 이 시멘타이트는 탄소와의 화합물이므로 탄화물이라고 하며, 전술한 고용체와는 근본적으로 다른 상이다. 즉 페라이트나 오스테나이트와 같은 고용체는 일반적으로 온도에 따라 용질원소인 탄소의 고용한계가 변화되지만 시멘타이트는 어느 온도에서건 항상 중량%로 6.67%(원자%로는 25%)의 탄소를 가지고 있다. 이와 같이 성분금속원자들이 비교적 간단한 정수비로 결합되고, 복잡한 결정구조를 가지는 합금을 금속간화합물(金屬間化合物, intermetallic compound)이라고 하며, 경도가 높고 매우 취약한 특징을 갖고 있다. |
◆ 침입형자리(interstitial site) 페라이트나 오스테나이트나 결국 모두 Fe격자내에 탄소원자가 함유되어 있는 침입형 고용체이고, 용매원자인 Fe격자사이의 틈자리에 탄소가 존재한다는 것도 알았다. 그런데 여기서 우리는 실제로 탄소원자가 존재하는 자리가 어딘지를 알 필요가 있다.

8면체틈자리와 4면체틈자리의 크기에는 큰 차이가 있다. 표 1.2는 FCC와 BCC의 침입형자리와 그 크기를 나타낸 것이다. 철원자의 형상이 구형이고 서로 접촉해 있다고 가정할 때 오스테나이트(FCC)에서 8면체틈자리의 크기(반경)는 0.52Å이지만, 4면체틈자리의 크기는 0.28Å에 불과하다. 즉 오스테나이트에는 4면체틈자리보다 8면체틈자리에 침입형원자가 침입하기 쉽다는 것이다. 따라서 탄소원자는 8면체틈자리에 쉽게 침입할 수 있지만, 이 틈자리의 크기(0.52Å)보다 탄소원자의 반경(0.7Å)이 더 크기 때문에 격자팽창을 피할 수는 없다. 한편 표 1.2에서 알 수 있는 바와 같이 페라이트에서의 침입형자리의 크기는 오스테나이트에서보다 훨씬 작다. 즉 8면체틈자리의 크기는 0.19Å, 4면체틈자리의 크기는 0.35Å에 불과하다. 이와같이 BCC구조인 페라이트내의 침입형자리의 크기가 작기때문에 오스테나이트보다 탄소를 수용하기가 어려워진다. 따라서 앞 절에서 언급한 바와 같이 페라이트내에 탄소의 고용한계는 오스테나이트에서보다 훨씬 작을 수밖에 없는 것이다. 만일 오스테나이트의 8면체틈자리(0.52Å)에 존재하는 많은 탄소원자가 급랭시에 BCC의 8면체틈자리(0.19Å)에 갖혀 있게되면 격자변형은 피할 수 없게 되어 결국 입방정구조(cubic structure)가 정방정구조(tetragonal structure)로 변하게 된다. 이렇게 해서 형성된 조직을 우리는 마르텐사이트(martensite)라고 부르며, 강을 경화시키기 위한 열처리의 궁극적인 목적은 바로 이 마르텐사이트조직을 형성시키기 위한 것이다.
|
◆ 결정립 금속의 결정구조는 극히 미시적인 크기의 단위이므로 현미경을 통해서는 볼 수 없고 X선 회절을 통해서 그 형태를 확인할 수 있을 뿐이다. 그러나 금속의 한면을 경면(鏡面)상태로 연마한 후 나이탈(nital)과 같은 산으로 부식시키면 조직을 관찰할 수 있다. 이 조직을 보면 무수히 많은 작은 입자들이 모여서 금속을 이루고 있다는 것을 알 수 있다. 이 하나하나의 입자를 결정립(結晶粒, grain)이라 하고, 결정립간의 경계를 결정립계(結晶粒界, grain boundary)라고 부른다. ⑴ 결정립 형성과정 이 결정립 형성과정의 초기단계에서는 소위 "결정핵"의 형성이 있게되는데 액체의 온도가 응고점에 도달하자마자 용액의 일부에서는 이 결정핵이 형성되기 시작한다. 형성된 결정핵이 성장하면서 용해잠열이 방출되고, 이 열이 외부로 전달되면서 결정핵은 결국 인접한 결정과 부딪칠 때까지 계속 성장한다. 이렇게 생성된 결정립계 부위에서는 원자배열의 불규칙도가 크며, 이때의 불규칙도는 응고가 진행됨에 따라 잔류용액에 농축되는 용질원소가 많아질수록 더욱 커진다. 결정립계가 흔히 내부식성이 가장 약한 이유는 바로 이러한 원자의 불규칙배열에 의한 것이다. 따라서 결정립계는 금속재료분야에서 하나의 결함(면결함)으로 분류되지만 다음에 서술되는 기계적성질에는 매우 큰 영향을 미친다. ⑵ 결정립크기와 기계적성질 결정립크기는 금속의 종류, 불순물 등에 의해서 영향을 받는다. 그림 1.10의 ⒜는 순철, ⒝는 저탄소강의 페라이트조직을 동일한 배율(100배)로 나타낸 것으로, 탄소가 소량 함유된 저탄소강의 결정립이 훨씬 미세하다는 것을 알 수 있다. 또한 결정립크기는 냉각속도에도 관계하는데, 일반적으로 냉각속도가 클수록 결정립은 미세해진다. 이러한 결정립의 크기에 따라 기계적성질에 많은 영향을 주는데, 항복응력과 결정립크기와의 사이에는 다음과 같은 관계식이 성립된다. (5-10) 여기서 = 항복강도 = 입내에서 전위의 이동을 방해하는 마찰응력 = 상수 = 결정립의 직경 이 식을 Hall-Petch 관계식이라 하는데, 대부분의 결정질 재료의 항복강도는 결정립크기가 미세할수록 증가한다는 것을 나타내고 있다. 이와같이 결정립이 미세할수록 금속의 항복강도뿐만 아니라 피로강도 및 인성이 개선되므로 실제로 금속재료분야에서 결정립의 미세화는 매우 중요한 기계적성질 개선책으로 이용되고 있다. |
● 확산 전술한 바와 같이 열처리란 금속내에 상변태를 일으켜서 기계적성질의 개선을 도모하는 조작방법이다. 그리고 강의 열처리시 나타나는 상변태는 후술하는 마르텐사이트변태만을 제외하고는 모두 확산을 동반하는 변태이므로, 열처리에 대한 기초지식으로서 확산에 대한 기본개념을 파악하는 것도 매우 중요하리라 생각된다. 일반적으로 액상이나 고상내에서 어느 성분의 농도차가 존재하면 그 성분은 농후한 부분으로부터 희박한 부분으로 이동하게 되는데, 이것을 확산(擴散, diffusion)이라고 한다. |
◆ 확산기구(mechanisms of diffusion) 그러면 실제로 금속내에서 원자들은 어떻게 이동하는가? 이에 대한 기구로서는 여러가지가 있지만 여기서는 가장 일반적인 기구인 침입형 확산기구(侵入型擴散機構, interstitial mechanism)와 공공 확산기구(空孔擴散機構, vacancy mechanism)에 대해서만 알아보기로 한다. ⑴ 침입형기구 어느 침입형자리에 위치하는 침입형원자가 용매원자들의 위치는 변화시키지 않고 최인접 침입형자리로 이동하는 기구를 침입형기구라고 한다. 그림 1.1(a)는 FCC 격자의 (100) 면에서의 침입형원자를 나타내는 것이다. 침입형원자 1이 침입형자리 2로 이동하기 위해서는 용매원자인 3과 4가 약간씩 바깥쪽으로 이동되어야만 한다. 즉 침입형원자가 인접한 침입형자리로 이동하기 위한 통로가 마련되어야만 한다. 이와 같은 장애물이 극복되는 속도가 결국 침입형원자의 확산속도를 결정해주는 것이다. 따라서 이 침입형기구에 의해서 확산하려고 하는 원자는 용매원자에 비해서 크기가 작아야만 용이하고, 실제로도 탄소(C)나 질소(N)와 같이 비교적 크기가 작은 침입형원자의 확산이 이 기구를 통해서 이루어지고 있다. 즉 강에서 일어나는 탄소의 이동은 전적으로 침입형확산이라 할 수 있고, 이 침입형기구에 의한 확산은 후술하는 공공기구에 의한 확산보다 비교적 용이하게 일어난다. ⑵ 공공기구 절대온도 0oK(-273℃)에서 금속결정은 결정격자에 완전히 원자가 배열된 상태로 되어 있다. 그러나 온도가 상승하면 원자가 격자점으로부터 방출되어 비어있는 격자점이 생기게 된다. 이와같이 원자가 방출되어 비어있는 격자점을 공공(空孔, vacancy)이라고 한다. 이 공공에 인접한 어떤 원자가 공공으로 점프하여 이동할 때 공공기구에 의해서 확산하고 있다고 말한다. 그림 1.1(b)는 FCC 격자에서 공공에 인접한 원자가 공공으로 점프하여 이동하는 과정을 보여주는 것이다. 원자직경을 라 할 때 1번 원자와 2번 원자 사이의 간격은 0.73이므로 주어진 원자가 그림의 화살표와 같이 인접한 공공으로 이동할 때 요구되는 1번 원자와 2번 원자의 변위는 그다지 크지 않다. 그럼에도 불구하고 공공기구에 의해서 확산하는 철원자가 침입형기구에 의해서 확산하는 탄소원자에 비해서 훨씬 느리게 확산하는 이유는 탄소원자 주위에는 침입형자리가 항상 존재하지만 철원자 주위에 공공이 존재할 확률은 희박하기 때문이다. 
그림 1.1 확산기구의 개략도 (a) 침입형기구 (b) 치환형기구 |
◆ 확산의 이용 전술한 바와 같이 강의 열처리는 상변태를 일으키는 조작방법이고, 또한 강의 상변태는 무확산변태(無擴散變態, diffusionless transformation)마르텐사이트변태만을 제외하고는 확산을 동반하는 확산변태(擴散變態, diffusional transformation)이므로 매우 중요한 현상이다. 특히 표면경화처리방법으로서 매우 널리 행하여지고 있는 침탄(浸炭, carburizing)이나 질화(窒化, nitriding)처리는 확산현상을 직접 이용하는 방법이므로 실제적인 관점에서나 확산의 관점에서나 그 중요성은 매우 크다. 이외에도 석출(시효 또는 템퍼링시), 확산풀림(균질화풀림) 및 결정립성장 등도 확산과 직접적으로 관련되는 현상이다. |
◆ 확산에 영향을 주는 인자 확산에 영향을 미치는 인자는 여러가지가 있다. 첫째로, 온도가 높아짐에 따라 원자의 움직임이 활발해지므로 확산속도가 빠르게 되고, 또 가공변형이 있는 경우에 확산은 용이하게 일어난다. 특히 조직이나 첨가원소의 종류나 양에 따라서 확산속도가 변화된다. 예를 들면 α철보다 γ철에서 탄소가 확산하는 것이 더 용이하다. |
● 변태와 조직 ◆ 변태와 변태점 일상생활에서 사용되는 변태란 용어와는 달리 금속에서는 급작스런 변화 즉 금속의 결정구조가 변화되는 것을 변태(變態, transformation)라고 한다. 순철을 가열하면 α철은 점차로 팽창하다가 어느 온도(A3변태점)에 도달하면 갑자기 수축을 일으키게 된다. 이 갑작스런 변화(변태)는 전술한 결정구조의 변화에 의해서 일어나는 것이다. 변태를 일으키는 온도를 변태점(變態点, transformation temperature)이라고 부른다. |
◆ 강의 5가지 변태 강에서는 A0, A1, A2, A3 및 A4의 5가지 변태가 있다. 이중에서 A3변태는
α철(체심입방격자) ←----→ γ철(면심입방격자) 910℃
으로 나타내지는데, 전술한 바와 같이 결정구조가 변화된다. A1, A4변태도 결정구조의 변화이다. 따라서 이들 변태는 고체 내에서 원자배열의 변화를 일으켜야만 하므로 변태온도의 변동을 약간 초래한다. A3변태점을 예로 들면 가열시의 변태점을 Ac3, 냉각시의 변태점을 Ar3로 표시하여 구분한다. 첨자 c 및 r은 불어의 chauffage (가열), refroidissement (냉각)의 첫글자를 나타낸다. A2변태는 순철이 자성을 잃는 변태, A0변태는 시멘타이트가 자성을 잃는 변태를 말한다. 이들 변태는 결정구조의 변화를 수반하지 않으므로 결정구조의 변화를 수반하는 순수한 변태와 구별해서 자기변태(磁氣變態, magnetic transformation)라고 불리워진다. 한편 퀜칭할 때도 후술하는 바와 같이 A를 사용한 Ar', Ar''이라고 하는 변태가 있다. |
◆ 변태와 조직변화 변태는 결정구조의 변화이므로 결정립조직 즉 현미경조직도 변한다. 따라서 조직명의 첫글자에다가 start(개시)의 첫문자인 s를 붙여서 변태개시온도를 나타내고, finish(종료)의 첫문자인 f를 붙여서 변태종료온도를 나타낸다. 예를 들면 다음과 같다. Ms : 오스테나이트 → 마르텐사이트로의 변태개시 Mf : 오스테나이트 → 마르텐사이트로의 변태종료 Ps : 오스테나이트 → 펄라이트로의 변태개시 Pf : 오스테나이트 → 펄라이트로의 변태종료 강의 열처리와 관계가 깊은 변태는 특히 A1과 A3변태로서, 후술하는 철-탄소계 상태도는 탄소량에 따른 변태점의 변화를 그림으로서 나타낸 것이다. |
● 탄소와 합금원소의 역할 ◆ 강의 강도와 탄소 앞 절에서 강을 분류할 때 탄소량에 따라서 저탄소강, 중탄소강 및 고탄소강으로 분류하였지만 다음과 같이 분류하는 방법도 있다.
극연강 ------------ 0.2%C 이하 연 강 ------------ 0.2∼0.3%C 반경강 ------------ 0.3∼0.5%C 경 강 ------------ 0.5∼0.8%C 최경강 ------------ 0.8∼1.5%C
탄소가 철중에서 화합하면 시멘타이트(Fe3C)라고 하는 탄화물이 형성되는데, 이 시멘타이트는 비커스 경도 HV=1100정도로 매우 硬한 화합물이다. 더구나 1%의 탄소는 15%의 Fe3C를 형성하므로 이것이 탄소가 강을 硬하게 하는 이유이다. 강의 퀜칭경도는 탄소량이 증가함에 따라 커지지만 이것은 0.6%C까지만 해당되는 것이고, 이 이상 탄소량이 증가해도 퀜칭경도는 증가되지 않는다. 그림 1.2는 이것을 나타낸 것으로서, 약 0.6%C까지는 탄소량에 따라 퀜칭경도가 증가되지만 그 이상 탄소량이 증가하여도 HRC 65 이상으로는 되지 않는다. 
그림 1.2. 강의 탄소량과 퀜칭경도와의 관계 |
◆ 탄소량과 성질의 변화 탄소강의 성질은 기본적으로 탄소조성에 의해서 결정되며, 탄소량이 일정해도 가공상태나 열처리조건에 따라서 그 성질은 현저하게 변화된다. 본절에서는 표준상태의 탄소강의 성질에 관해서만 공부하기로 하고, 가공이나 열처리에 의한 성질변화는 다음 장에서 서술하기로 하자. 우선 표준조직이라고 하는 것은 탄소강을 A3 및 Acm 온도 이상 30∼50℃로 가열하여 균일한 오스테나이트로 만든 후 상온으로 공랭시켰을 때에 형성되는 조직으로서, 아공석강에서는 페라이트와 펄라이트, 공석강에서는 펄라이트, 그리고 과공석강에서는 시멘타이트와 펄라이트로 된다. ⑴ 물리적 성질과 화학적 성질 전술한 바와 같이 강은 페라이트와 시멘타이트(Fe3C)로서 이루어진 혼합조직을 갖고 있고, 이 조직의 혼합비율은 탄소량에 의해서 결정되기 때문에 탄소강의 물리적 성질은 탄소량에 따라 직선적으로 변화된다. 그림 1.3는 탄소강에서 탄소량에 따른 물리적 성질의 변화를 나타낸 것이다. 그림에서 보면 탄소강의 비중, 열팽창계수 및 열전도도는 탄소량이 증가함에 따라서 감소되지만, 비열, 전기저항 및 항자력은 증가된다. 한편 탄소강의 내식성은 탄소량이 증가될수록 감소하고, 소량의 Cu가 첨가되면 내식성이 향상된다. 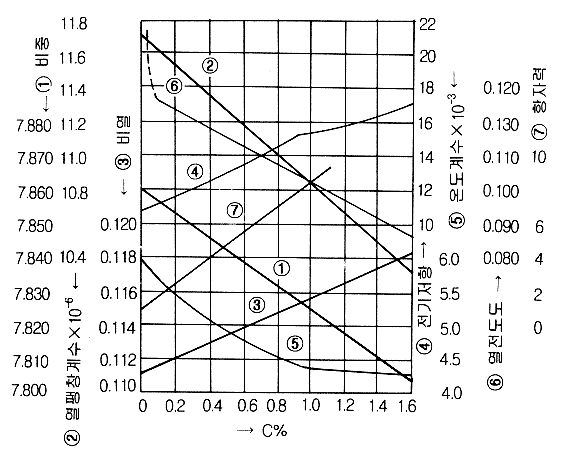
그림 1.3. 강의 물리적 성질변화 ⑵ 상온 기계적 성질 탄소강의 탄성계수(Young's modulus) E는 20000∼22000㎏/㎜2, 강성율(shear modulus) G는 7700∼8450㎏/㎜2, Poisson의 비 ν는 0.28로서 이들 상수들은 탄소량에 관계없이 거의 일정하다. 그러나 그림 1.4에서 보는 바와 같이 다른 기계적 성질들은 탄소량에 따라서 직선적으로 변화되는데, 아공석강에서의 인장강도, 경도 및 항복점 등은 탄소량에 따라 증가되고, 연신율 및 단면감소율은 탄소량에 따라 감소한다.

그림 1.4. 탄소강의 기계적 성질 및 조직의 관계 과공석강에서는 시멘타이트가 망상으로 나타나므로 탄소량이 증가함에 따라 인장강도는 오히려 감소한다. 그러나 경도는 계속해서 증가된다. 한편 이와 같이 탄소량에 따라 기계적 성질이 변화되는 것은 표 1.3에 나타낸 페라이트, 시멘타이트 및 펄라이트의 기계적 성질과 관련되어 있다. 즉 페라이트는 극히 연성이 크고 인장강도는 비교적 작다. 그리고 시멘타이트는 매우 경도가 높고 취약하여 인성은 거의 없으며, 펄라이트는 페라이트에 비해서 인장강도가 크고 경도가 높다. 따라서 아공석강에서 탄소량에 따라서 인장강도 및 경도가 증가되는 것은 펄라이트량의 증가에 기인한다는 것을 표로부터 짐작할 수 있고, 또한 과공석강에서 연신율이 감소하는 것은 연신율이 거의 0 인 시멘타이트 때문이라는 사실을 알 수 있다. 이것은 그림 1.4의 하단부에 탄소량에 따른 페라이트, 시멘타이트 및 펄라이트의 양적 비율과 기계적 성질을 관련시켜보면 쉽게 알 수 있다. 
표 1.3 페라이트, 시멘타이트 및 펄라이트의 기계적 성질 ⑶ 고온 기계적 성질
동일 성분의 탄소강이라도 온도에 따라 그 기계적 성질은 매우 달라진다. 그 예로서 0.25%C의 아공석 탄소강을 가지고 0∼500℃ 사이에서 일어나는 여러가지 기계적 성질의 변화를 그림 1.5에 나타냈다.

그림 1.5. 온도에 따른 탄소강의 기계적 성질 그림에서 보는 바와 같이 탄성계수, 탄성한계 및 항복점 등은 온도가 상승함에 따라 감소한다. 그리고 인장강도는 200∼300℃의 온도범위에서는 증가하여 최대가 되고, 연신율과 단면감소율은 온도상승에 따라 감소하다가 인장강도가 최대로 되는 온도에서 최소로 되고는 점차 다시 증가된다. 충격치는 200∼300℃에서 가장 적으므로 탄소강은 이 온도범위에서 가장 취약하게 된다. 이것을 청열취성(靑熱脆性, blue brittleness)이라 하며, 이 온도범위에서 가공하는 것은 피하는 것이 좋다. 상온 이하의 온도에서는 온도가 저하됨에 따라 인장강도, 경도, 탄성계수, 항복점 및 피로한계 등은 점차 증가하지만, 연신율, 단면수축율 및 충격치 등은 감소되어 성질이 취약해진다. 충격치는 온도저하에 따라 감소하다가 어떤 임계온도, 즉 천이온도(遷移溫度, transition temperature)에 도달되면 급격히 감소되어 -70℃ 부근에서는 거의 0 에 가까운 값을 갖는다. |
◆ 합금원소 첨가에 따른 강의 성질 변화 鋼중에는 제강(製鋼)과정에서 강의 제성질을 향상시키기 위해 고의로 첨가한 합금원소도 있지만, 이 이외에 선철(銑鐵), scrap 등의 원료로부터 혼입되는 미량의 잔류원소도 존재하는데, 이러한 잔류원소들이 강의 성질에 미치는 영향도 무시할 수 없다. 이러한 잔류원소들 중에서 Cu, Ni, Co, Sb, As, W, Mo, Sn 등은 제강시에 거의 제거할 수 없는 원소로서 강에 치환형으로 고용해있고, 강의 성질을 변화시키기 위해서는 비교적 다량첨가가 필요하다. 또한 C, H, N 등의 원소들은 제강시 일부 제거할 수 있는 원소들로서, 강에 침입형으로 고용해서 미량존재로도 강의 성질에 큰 영향을 미친다. 따라서 본절에서는 강에 함유된 여러가지 원소들이 강의 제성질에 미치는 영향을 요약하여 서술하였다. (1) 탄소(C) 탄소는 강의 강도를 향상시키는데에 가장 효과적이고 중요한 원소로서, 오스테나이트에 고용하여 퀜칭 열처리시 마르텐사이트 조직을 형성시키게 한다. 탄소량의 증가와 함께 퀜칭경도를 향상시키지만 퀜칭시 변형유발가능성을 크게 한다. Fe, Cr, Mo, V 등의 원소와 화합하여 탄화물을 형성하므로써 강도 및 경도를 향상시킨다. (2)망간(Mn) 탄소강에는 보통 0.35∼1.0% 정도의 Mn이 함유되어 있다. 이 Mn의 일부는 강 속에 고용되며, 나머지는 강 속에 함유되어 있는 S와 결합하여 비금속개재물(nonmetallic inclusion)인 MnS를 결정립내에 형성하는데, 이 MnS는 연성이 있어서 소성가공시에 가공방향으로 길게 연신된다. 그러나 이 MnS의 형성으로써 강 속의 S의 양이 감소되므로 결정립계에 형성되는 취약하고 저융점화합물인 FeS의 형성을 억제시킨다. 한편 Mn에 의해서 펄라이트가 미세해지고, 페라이트를 고용강화시키므로써 탄소강의 항복강도를 향상시킨다. 또 퀜칭시 경화깊이를 증가시키지만, 많은 양이 함유되어 있을 때에는 퀜칭균열이나 변형을 유발시킨다. 그리고 Mn은 강에 점성을 부여하므로 1.0∼1.5%Mn이 첨가된 강을 강인강(强靭鋼)이라고 부르며, 특히 1.3%C, 13%Mn이 함유된 오스테나이트강을 Hadfield鋼이라고 부르며 옛날로부터 유명한 강이다. 단 Mn은 강의 내산성(耐酸性) 및 내산화성(耐酸化性)을 저해하는 원소이다. (3) 황(S) 강 속에 함유되어 있는 S는 보통 Mn과 결합하여 MnS 개재물을 형성한다. 그러나 강 중의 Mn 양이 충분치 못할 때에는 Fe와 결합하여 FeS를 형성하기도 하는데, 일반적으로 이 FeS는 결정립계에 그물모양으로 석출되어 있다. 이 FeS는 매우 취약하고 용융점이 낮기때문에 열간 및 냉간가공시에 균열을 일으킬 수 있다. 따라서 해로운 FeS 개재물의 형성을 피하기 위해서는 Mn:S의 비를 보통 5:1로 하고 있다. 일반적으로 Mn, Zn, Ti, Mo 등의 원소와 결합하여 강의 피삭성을 개선시킨다. (4) 인(P) P는 강 속에 균일하게 분포되어 있으면 별문제가 없으나, 보통 Fe3P의 해로운 화합물을 형성한다. 이 화합물은 극히 취약하고 편석되어 있어서 풀림처리를 하여도 균질화되지 않고 단조, 압연 등의 가공을 하면 길게 늘어난다. 충격저항을 저하시키고, 템퍼링취성을 촉진하며, 또 쾌삭강에서는 피삭성을 개선시키는 원소로 취급되나, 일반적으로는 불순물로서 간주된다. (5) 규소(Si) 강 속의 Si는 선철과 탈산제에서 잔류되는 것으로, SiO2 와 같은 화합물을 형성하지 않는한 페라이트 속에 고용되므로 탄소강의 기계적성질에는 큰 영향을 미치지 않는다. 또한 P는 강한 탈산제이고, 4.5% 첨가량까지는 강도를 향상시키지만 2% 이상 첨가시에는 인성을 저하시키고 소성가공성을 해치므로 첨가량에 한계가 있다. 한편 템퍼링시 연화저항성을 증대시키는 효과도 있다. (6) 질소(N) 강 중에 잔류하는 질소량은 용해원료, 용해방법에 따라서 현저하게 변화된다. 일반적으로 질소는 극히 미량 존재로도 강의 기계적성질에 큰 영향을 미치는데 인장강도, 항복강도를 증가시키고, 연신율을 저하시킨다. 특히 충격치의 감소 및 천이온도의 상승은 현저하다. 질소는 탄소와 동일하게 침입형원소이고, 강중에서 확산속도가 빠르며, 또한 페라이트에 대해서 최대 약 0.1%(580℃)로부터 0.003%정도(상온)까지 연속적으로 용해도변화를 나타내는 등 다른 잔류원소와는 틀리는 큰 특징이 있다. 이때문에 강은 각종의 취성이나 시효경화성을 나타낸다. 퀜칭시에 일어나는 퀜칭시효(quench aging), 냉간가공에 의한 변형시효(strain aging), 그리고 200∼300℃에서의 청열취성에 의해서 강의 인장강도, 항복강도는 증가하고 충격치는 저하해서 강의 취화를 일으킨다. 특히 극연강 박판의 deep drawing 가공시에 표면에 주름이 발생하는 현상은 주로 질소의 변형시효에 의한 것이다. 이것을 안정화시키기 위해서는 질소와 친화력이 큰 Al, Ti, Zr, V, B 등을 첨가하므로써 이들의 취화현상을 방지한다. 또 질소는 다른 합금원소와 결합하여 질화물을 형성하므로 강의 여러성질에 영향을 미친다. AlN이 강중에 미세하게 석출되어 있으면 오스테나이트의 결정립이 미세하게 되어 세립강(細粒鋼)의 제조가 가능하고, 이외에 Ti, Zr, V, Nb 등도 질화물을 형성하여 결정립을 미세하게 만든다. 그러나 AlN도 다량 존재하면 고온인성을 크게 해치고, 특히 단조시에는 오스테나이트 입계에 AlN이 석출하여 입계취성을 일으킨다. 또한 AlN의 석출에 의해 고온크리프강도도 저하된다. (7) 수소(H) 수소는 원자반경이 극히 작으므로 Fe격자중에 N, C 등과 동일하게 침입형으로 고용되어 있고, 강중에서는 다른 원소에 비해서 확산속도가 매우 빠르므로 강속을 자유로이 이동할 수 있다. 또 수소는 백점(白点), 헤어 크랙(hair crack), 선상 조직(線狀組織) 및 용접시 비드 균열 등 여러가지 결함의 원인으로 된다. 이러한 결함의 방지 또는 제거를 위하여 최근에는 진공용해 또는 진공처리에 의해 탈수소를 행하고 있으므로 제강과정에서 생긴 수소에 의한 결함은 감소되고 있다. (8) 산소(O) 산소는 거의 Fe에 고용되지 않기때문에 강중에서는 주로 비금속개재물로서 존재하며, 이들중 SiO2, Al2O3, Cr2O3, TiO2 등은 Fe에 대해서 고용도를 갖지 않지만 FeO, MnO 등은 고온에서 약간 고용한다. 특히 이들 비금속개재물은 강의 기계적성질, 피로특성 등을 저하시킨다. 순도가 높은 Fe-O 합금에서는 산소함유량의 증가와 함께 충격천이온도는 현저하게 상승하지만, 순철에 소량의 C, Mn 등이 존재하면 그 영향은 거의 사라진다. 산소는 다량으로 함유되어 있으면 강의 침탄시 이상조직의 원인으로 됨과 동시에 경화능을 저하시키고, 가열에 의한 오스테나이트 결정립의 성장을 촉진시킨다. (9) 구리(Cu) Cu는 광석 등으로부터 쉽게 혼입되므로 강에는 보통 0.1∼0.3% 정도 함유되어 있다. Cu는 상온에서 페라이트에 0.35%까지 고용하여 고용강화효과를 나타내므로 강도 및 경도를 약간 증가시키지만 연신율은 저하시킨다. Cu를 함유한 강에서는 열간가공성이 문제로 되는데, 특히 0.5%이상 함유되어 있을 때에는 적열취성(赤熱脆性, red brittleness)의 원인으로 된다. 이것은 고온가열시에 Fe보다 Cu의 산화속도가 작으므로 강표면에 편재하여 열간가공중에 강재 내부로 침투하기 때문이지만, Ni이나 Mo의 첨가로서 이 현상을 현저히 개선할 수 있다. 또한 Cu는 비교적 소량 함유되어 있어도 대기 및 해수중에서 강의 내식성을 현저하게 향상시킨다. Cu와 P가 공존할 경우 내식성향상에 더욱 효과적이다. 한편 0.4%Cu 이상 첨가시에는 Cu의 미세석출에 의한 석출경화효과도 나타나므로, 실제로 스테인리스강에서는 Cu를 4%정도 첨가석출시켜서 강력 스테인리스강도 만들고 있다. (10) 알루미늄(Al) Al은 강탈산제로서 유효하나 첨가량이 많으면 강을 취약하게 함으로 탈산, 탈질용으로서는 0.1%이하로 첨가하는 것이 보통이다. 질화물인 AlN은 미세석출하여 강의 결정립미세화에 효과적이므로 이것을 이용해서 극미세 결정립을 갖는 강인강을 제조할 수 있다. 또한 고온산화방지 및 내유화성(耐硫化性)에 극히 효과적이다. (11) 비소(As) As는 제선제강과정에서 제거하는 것이 거의 불가능하고, 또 강재의 재질향상을 위해서 As를 인위적으로 첨가하는 경우는 거의 없다고 보아도 좋다. 즉 As는 0.2%정도 이상에서는 충격치를 현저하게 저하시키고, 충격천이온도를 상승시킴과 함께 강의 열간가공성을 해치고 적열취성을 일으킨다. 그러나 이러한 악영향은 보통강에 함유되어 있는 정도의 As량에서는 거의 문제시 되지 않는다고 보아도 좋다. (12) 붕소(B) 미량 첨가(0.0005∼0.003%)로서 경화능을 현저히 증가시킨다. 과잉 첨가되면 Fe3B를 형성하여 적열취성을 일으킨다. (13) 코발트(Co) 대부분의 합금원소는 소량첨가로써 강의 경화능을 향상시키지만 Co는 예외로서 그 반대의 경향을 나타내고, 또 고가이므로 일반적인 강에는 사용하지 않고 자석, 고급절삭공구, 내열재료 등에 첨가해서 성질을 개선하는데에 사용하고 있다. 특히 강의 고온강도를 개선하는데에 효과적이다. (14) 크롬(Cr) 13%까지 첨가로서 오스테나이트 영역을 확장시킨다. 염가이고, 다량 첨가해도 취화를 일으키지 않는 탄화물을 형성시킨다. 10%이상 첨가하면 스테인리스강으로 되고, 내산화성을 향상시키고 내유화성을 개선하므로 구조용강, 공구강, 스테인리스강 및 내열강의 거의 전부에 함유되어 있는 가장 중요하고 보편적인 합금원소이다. 단 Cr첨가량이 많게 되면 σ상이라고 하는 비자성의 취약한 상이 나타난다. Cr은 또한 저온취성과 수소취성을 방지하는 효과가 있지만 템퍼링취성은 조장한다. (15) 몰리브덴(Mo) Mo은 0.1∼0.3%정도의 첨가로서 Ni의 10배까지 경화능을 향상시키는 효과가 있으므로 템퍼링취성을 방지하여 템퍼링취화저항성을 부여한다. 또한 탄화물을 형성하므로 고급절삭공구의 합금원소로도 우수한 효과를 나타내며, 결정립조대화온도를 상승시킨다. 경화능에 관해서는 Mo 단독보다는 Cr과 병용하면 더욱 효과적이다. 값이 비싸다. (16) 니켈(Ni) Ni은 강의 조직을 미세화시키고, 오스테나이트나 페라이트에도 고용이 잘되므로 기지를 강화시킨다. 또 Cr이나 Mo과의 공존하면 우수한 경화능을 나타내어 대형강재의 열처리를 용이하게 한다. Ni은 오스테나이트 안정화원소이므로 Cr과의 조합으로 오스테나이트계 스테인리스강, 내열강을 형성한다. 강의 저온인성을 현저히 개선시키며 용접성, 가단성(可鍛性)을 해치지 않는다. 또한 Ni은 C나 N의 확산을 느리게 하므로 내열강의 열화(劣化)를 방지하고, 팽창률, 강성률, 도자율(導磁率) 등의 점에서도 특징이 있다. 즉 Fe-36%Ni강은 상온부근에서의 열팽창계수가 0에 가까우므로 전자재료(電磁材料) 및 특수재료로서의 용도가 넓다. 따라서 Ni은 Cr과 함께 가장 중요하고도 보편적인 합금원소이다. (17) 티타늄(Ti) Ti은 O, N, C, S 및 H 등 어느 원소와도 강한 친화력을 나타내고, 특히 탈산, 탈질(脫窒) 및 탈유(脫硫)에 흔히 사용된다. 탄화물형성능도 Cr보다 강하고, 결정립을 미세화시키기때문에 스테인리스강이나 절삭공구강의 개량에 이용된다. 또한 타금속원소와도 화합물을 형성하여 석출경화효과가 현저하므로 석출경화형 스테인리스강이나 영구자석 등에 이용된다. (18) 주석(Sn) Sn은 scrap으로부터 혼입되어 제강과정에서는 거의 제거되지 못하는 원소로서, 페라이트에는 약 8%까지 고용한다. 일반적으로 Sn은 강의 인장강도, 항복강도를 증가시키고, 연신율, 충격치를 감소시키는 등 P의 영향과 유사한 점이 많지만 P만큼 현저하지는 않다. 그러나 Sn은 열간가공시의 적열취성, 템퍼링취성, 저온취성 등의 원인으로 되고, 내식성에 약간의 이점이 있기는 하지만 일반적으로 강에는 유해한 원소이다. (19) 셀레늄(Se) Mn 등과 화합물을 만들어 피삭성을 향상시킨다. 유황보다 훨씬 고가이며 용강(熔鋼)의 유동성을 좋게 한다. (20) 칼슘(Ca) 강력한 탈산제이다. 용강중에서 기화하여 폭발하기 쉬우므로 Ca-Si, Ca-Si-Mn 등의 상태로 첨가하여 비금속개재물의 상태 및 분포의 조정을 행한다. (21) 니오븀(Nb) 강력한 결정립 미세화원소로서 결정립 조대화온도를 상승시킨다. 경화능을 저하시키며, 템퍼링취성을 감소시킨다. (22) 텔루륨(Te) 강의 피삭성을 증대시키며, 열간가공성을 해친다. (23) 납(Pb) 강의 피삭성을 향상시킨다. (24) 바나듐(V) 탄화물 형성능이 커서 미립탄화물을 만들어 강의 조직을 미세화시키므로 고장력강으로부터 각종 공구강에 이르기까지 많이 사용되고 있다. 템퍼링연화저항성도 Mo이상으로 좋다. 고온강도도 대폭 향상시키지만 산화물인 V2O5는 증기압이 높아서 고온증발하므로 첨가량에 한계가 있다. (25) 텅스텐(W) W은 고가이고, 비중이 커서 편재하기 쉬우므로 구조용강에는 거의 첨가되지 않지만, 경화능을 향상시키고 Fe4W2C 또는 Fe3W3C형의 탄화물을 형성하므로 공구강 특히 절삭공구강에 이용되고, 18%W-4%Cr-1%V강은 고속도강으로서 유명하다. 또 W이 함유된 자석강도 있다. (26) 지르콘(Zr) N, S, C 및 H와의 친화력은 Ti보다 더욱 강하기때문에 이들 원소의 고정에 흔히 이용되고 있다. 백점의 발생도 0.2∼0.3%첨가로 완전히 방지할 수 있다고 알려져 있다. 참고문헌 1. 延倫模, 池武晟, 宋鍵, 洪英煥 : 金屬材料, 機電硏究社, 1994 2. 歌川 寬 : やさしい 金屬熱處理技術の基礎, 啓學出版, 1981 3. G. Krauss : Principles of Heat Treatment of Steels, American Society for Metals, Metals Park, Ohio, 1980 4. C. R. Brooks : Heat Treatment of Ferrous Alloys, McGraw-Hill, New York, 1979 5. 日本熱處理技術協會 : 熱處理の基礎(Ⅰ), 日刊工業新聞社, 1970 6. P. G. Shewmon : Diffusion in Solids, McGraw-Hill, New York, 1963 7. C. R. Barrett, W. D. Nix, and A. S. Tetelman : The Principles of Engineering Materials, Prentice-Hall, New Jersey, 1973 8. L. E. Samuels : Optical Microscopy of Carbon Steels, American Society for Metals, Metals Park, Ohio, 1980 9. 金屬熱處理技術便覽編輯委員會 : 金屬熱處理技術便覽, 日刊工業新聞社, 1961 10. P. M. Unterweiser, H. E. Boyer, and J. J. Kubbs : Heat Treater's Guide, American Society for Metals, Metals Park, Ohio, 1982 11. C. S. Barrett and T. B. Massalski : Structure of Metals, 3rd Ed. McGraw-Hill, New York, |
■ 강의 열처리 기초 강은 열처리를 통하여 매우 다양한 미세조직과 성질이 얻어지기 때문에 열처리변수의 적절한 조합에 의해서 우리가 원하는 미세조직과 성질을 얻을 수 있다. 여기서 최종적인 미세조직과 성질을 결정해주는 기본적인 열처리변수는 첫째로, 어느 온도로 가열할 것인가 ? 둘째로, 이 온도에서 얼마동안 유지할 것인가 ? 셋째로, 냉각은 얼마나 빨리 할 것인가 ? 하는 등의 3가지가 있다. 이러한 변수들을 결정해 주기 위한 자료로서 매우 중요한 역할을 하는 것이 평형상태도(平衡狀態圖, equilibrium phase diagram)이다. 이 상태도는 특히 첫번째 변수인 열처리온도를 결정하는 데에는 없어서는 안될 결정적인 자료가 된다. |
● 상태도 ◆ 상태도의 기본적인 의미 상태도란 여러가지 조성의 합금을 용융상태로부터 응고되어 상온에 이르기까지 상태의 변화를 나타낸 그림을 말한다. 즉 합금의 성분비율과 온도에 따른 상태를 나타내는 그림으로서, 횡축에는 조성(%), 종축에는 온도(℃)로서 표시하고 있다. 그런데 여기서 횡축의 조성 즉 성분비율을 나타내는데에는 중량비율(wt%)이 보통 사용되지만 경우에 따라서는 원자비율(at%)로 나타낼 때도 있다. 이들의 상관관계는 다음절에서 자세하게 나타냈다. |
◆ 농도표시법 전술한 바와 같이 일반적으로 합금의 조성은 중량비율로서 나타낸다. 만일 어떤 합금 100g이 80wt%A와 20wt%B로 되어 있다면 이는 80g의 A와 20g의 B를 함유한 것이 된다. 한편 이론적인 계산을 하는 경우에는 원자수의 비율로서 농도를 표시하는 원자비율를 사용하는 일이 있다. 80at%A와 20at%B로 되어 있는 합금에서 A와 B의 원자비는 80:20=4:1이 된다. 따라서 우리는 중량비율을 원자비율로, 원자비율을 중량비율로 환산해야만 할 때가 많이 있다. 이 wt%와 at%와의 사이에는 다음의 관계가 성립한다.   여기서 : 각각 A성분과 B성분의 중량% : 각각 A성분과 B성분의 원자% : 각각 A성분과 B성분의 원자량 한 예로 Sn의 원자량 Sn=118.69 120이며 Pb의 원자량 Pb=207.19 210이다. Pb의 at% XPb=30%라 할 때 Pb의 중량비율 WPb는  가 된다. |
◆ Fe-Fe3C 상태도와 상 순철은 910℃이하에서는 체심입방격자이고, 910℃ 이상1390℃까지는 면심입방격자이다. 여기에 탄소원자가 함유되면 두가지의 변화가 나타난다. 즉 변태온도가 낮아지고 변태가 단일온도에서 일어나는 것이 아니라 어느 온도범위에 걸쳐서 일어나게 된다. 이러한 내용이 그림 2.1에 잘 나타나 있다. 엄격하게 말해서 시멘타이트(Fe3C)로 불리우는 금속간화합물은 평형상이 아니기 때문에 이 상태도는 엄밀하게 말하면 평형상태도가 아니다. 어떤 조건하에서 시멘타이트는 더욱 안정한 상인 철과 흑연으로 분해될 수 있다. 그러나 Fe3C는 한번 형성되기만 하며 실질적으로 매우 안정하므로 평형상으로 간주된다. 이러한 이유로 인해서 그림 2.1의 상태도는 준안정 상태도이다. 상(相, phase)이라는 것은 물리적, 화학적 그리고 결정학적으로 균일한 부분을 말하는 것으로, 이것은 뚜렷한 계면에 의해서 합금의 다른 부분과 구분된다. Fe-Fe3C 상태도에 나타나는 고상의 종류에는 4가지가 있다. 즉, α페라이트(ferrite), 오스테나이트(austenite), 시멘타이트 및 δ 페라이트등이다. 이 각각의 상들을 구체적으로 나타내면 다음과 같다. 
그림 2.1. Fe-C상태도 (실선:Fe-Fe3C 상태도, 점선:Fe-C상태도) (1) α 페라이트 α철에 탄소가 함유되어 있는 고용체를 α 페라이트 또는 단순히 페라이트라고 부르며, BCC 결정구조를 가지고 있다. 상태도에서 나타내듯이 α 페라이트의 최대탄소고용도는 723℃에서 0.02%이므로 페라이트에 고용할 수 있는 탄소량은 매우 적은 것을 알 수 있다. 또한 α 페라이트의 탄소고용도는 온도가 내려감에 따라서 감소하여 0℃에서 약 0.008%정도이다. 탄소원자는 철원자에 비해서 비교적 원자크기가 작으므로 철의 결정격자내의 침입형자리(interstitial site)에 위치한다. 침입형자리는 4면체 틈자리(tetrahedral site)와 8면체 틈자리(octahedral site)의 두종류가 있는데, BCC인 α 페라이트에서는 4면체 틈자리인 의 크기가 크고, 그 침입형자리에 들어갈 수 있는 구의 최대반경은 0.35Å이다. 따라서 0.77Å의 반경크기를 갖는 탄소원자가 이 침입형자리에 들어가게 되면 탄소원자의 크기가 침입형자리보다 상대적으로 매우 크기 때문에 격자변형을 일으키게 된다. 이것이 α 페라이트내의 탄소고용도를 적게 하는 중요한 이유이다. (2) 오스테나이트 γ철에 탄소가 고용되어 있는 고용체를 오스테나이트(austenite)라고 하며, FCC 결정구조를 가지고 있다. 탄소고용도는 그림 2.1에서 볼 수 있듯이 1148℃에서 2.08%로 최대이며, 온도가 내려감에 따라서 감소하여 723℃에서 0.8%로 된다. 따라서 탄소고용도는 α 페라이트보다 매우 크다. 또한 α 페라이트에서와 마찬가지로 오스테나이트중의 탄소는 침입형자리에 위치하는데, FCC의 8면체 틈자리인 및 의 크기가 8면체 틈자리인 보다 크고, 8면체틈자리에 들어갈 수 있는 구의 최대반경은 0.51Å이다. 그러므로 0.77Å의 반경을 갖는 탄소원자가 8면체틈 자리에 들어가면 α 페라이트에서와 마찬가지로 격자변형을 일으키게 되지만, 그 변형정도는 α 페라이트보다는 작다. 이것이 오스테나이트의 탄소고용도가 α 페라이트보다 크게 되는 중요한 이유이기도 하다. 한편 이와 같이 오스테나이트와 α 페라이트의 탄소고용도가 차이나기 때문에 대부분의 강을 경화열처리하는데 있어서의 중요한 근거가 되는 것이다. (3) 시멘타이트 철탄화물(Fe3C)인 시멘타이트는 고용체라기보다는 금속간화합물로서, 6.67%의 탄소를 함유하고 있다. 결정구조는 그림 2.2와 같이 단위격자당 12개의 Fe원자와 4개의 C원자를 가지는 사방정(orthorhombic)이고, 매우 硬하고 취약한 성질을 가지고 있다. 
그림 2.2 시멘타이트(Fe3C)의 원자구조 (●:탄소원자, ○:철원자) (4) δ페라이트 δ철의 탄소고용체를 δ페라이트라고 하며, α 페라이트와 마찬가지로 BCC 결정구조를 가지지만 격자상수가 다르다. δ페라이트내의 최대탄소고용도는 1495℃에서 0.09%이다. |
◆ Fe-Fe3C 상태도의 해설 탄소는 철과 화합하여 시멘타이트(Fe3C)의 형태로 되는 경우와 또는 탄소單體의 흑연(黑鉛, graphite)으로 되는 경우가 있다. 강의 경우는 주로 시멘타이트의 형태로 존재하지만 주철에서는 흑연과 시멘타이트의 두가지 형태가 나타난다. 보통 시멘타이트는 고온으로 가열하면 철과 흑연으로 분해되므로 준안정상이라고 할 수 있고, 오히려 흑연이 안정상으로 간주된다. 그림 2.1중에서 실선이 Fe-Fe3C계 상태도를 나타내고, 점선이 철-흑연계 상태도를 나타내는 것이다. 철-흑연계 상태도는 주철에서 주로 고려되는 것이므로 여기서는 Fe-Fe3C 상태도에 대하여만 설명하고자 한다. 한편 실제 열처리작업에서 1200℃ 이상을 사용하는 경우가 극히 드물지만 참고적으로 함께 설명하였다. 특히 1200℃ 이하의 부분은 그림 2.3에서 구체적으로 설명하였다. 
그림 2.3. Fe-Fe3C계 평형상태도와 변형조직도 - A
| - :
| - 순철의 용융점 (1538℃)
| - N
| - :
| - 순철의 A4 변태점, δ철
γ철 (1394℃)
| - AB
| - :
| - δ페라이트의 액상선(응고가 시작되는 온도)
| - AH
| - :
| - δ페라이트의 고상선(응고가 종료되는 온도)
| - HN
| - :
| - δ페라이트가 오스테나이트로 변태하기 시작하는 온도
| - JN
| - :
| - δ페라이트가 오스테나이트로의 변태를 종료하는 온도
| - HJB
| - :
| - 포정선(1495℃, J점 ; 0.17%C, B점 ; 0.53%C), 이 온도에서 δ페라이트(H) + 액상(B)
오스테나이트(J)의 포정반응이 일어난다.
| - BC
| - :
| - 오스테나이트의 액상선
| - JE
| - :
| - 오스테나이트의 고상선
| - CD
| - :
| - 시멘타이트의 액상선
| - ECF
| - :
| - 공정선, 이 온도에서 액상(C)
오스테나이트(E) + Fe3C(F)의 공정반응에 의해서 액상으로부터 오스테나이트와 시멘타이트가 동시에 정출한다.
| - C
| - :
| - 공정점(1148℃, 4.3%C), 이 조성의 합금은 공정조직인 레데뷰라이트 (ledeburite)로 된다.
| - E
| - :
| - 오스테나이트에 대한 탄소의 최대고용한(1148℃, 2.11%C), 이 조성으로 강과 주철을 구분하고 있다.
| - ES
| - :
| - 오스테나이트로부터 시멘타이트가 석출하기 시작하는 온도를 나타낸다. Acm선이라고 부른다.
| - G
| - :
| - 순철의 A3 변태점, γ철
α철(912℃)
| - GS
| - :
| - 오스테나이트로부터 페라이트가 석출하기 시작하는 온도. A3선이라고 부른다.
| - S
| - :
| - 공석점 (0.77%C, 727℃)
| - PSK
| - :
| - 공석선, 이 온도에서 오스테나이트(S) 페라이트(P) + Fe3C(K)의 반응에 의해 펄라이트를 만든다. A1선(727℃)이라고 부른다.
| - GP
| - :
| - 오스테나이트로부터 페라이트로의 변태가 종료되는 온도.
| - P
| - :
| - α철에 고용하는 탄소의 최대고용도(727℃에서 0.02%C)
| - PQ
| - :
| - 페라이트에 대한 탄소의 용해도곡선. 상온에서 탄소고용도는 0.008% 이하이다.
| - M
| - :
| - 순철의 A2 변태점(자기변태점, 770℃).
| - MO
| - :
| - 강의 A2 변태점
|
|
● 탄소강의 변태 그림 2.3은 Fe-Fe3C 상태도의 일부로서, 강의 변태와 조직을 설명하는데 필요한 부분을 나타낸 것이다. 0.8%C를 함유하는 조성의 탄소강(S점)은 727℃ 이하로 냉각시 오스테나이트가 페라이트와 시멘타이트로 분해되는 공석반응을 일으키므로 공석강(共析鋼, eutectoid steel)이라고 하며, 이 반응이 일어나는 온도를 A1선 이라고 부른다. 또한 공석반응에 의한 변태를 공석변태, 펄라이트 변태, 또는 A1변태라고 부른다. 한편 0.8%C 이하의 탄소강을 아공석강(亞共析鋼, hypo-eutectoid steel)이라고 하는데, 공업적으로 생산되는 대부분의 강은 아공석강이다. 순철이 γ철로 변태하는 온도는 910℃(Ac3점)이지만 아공석강이 γ오스테나이트 단상으로 변태하는 온도는 GS선 이상이므로 이 GS선을 A3선이라고 한다. 또 0.8%C 이상의 탄소강을 과공석강(過共析鋼, hyper-eutectoid steel)이라고 부르는데, 과공석강에서는 SE선 이상으로 가열될 때 단상의 오스테나이트로 변태하므로 이 SE선을 Acm선이라고 부른다. 과공석강의 탄소함유량은 0.8∼2.0%C 범위이지만 공업적으로 생산되는 과공석강은 대부분이 0.8∼1.2%C 범위의 탄소량을 가지고 있다. 탄소량이 1.2% 이상이면 강의 성질이 매우 취약해지므로 거의 사용되지 않고 있다. 실제적으로 강을 변태시키기 위한 가열 및 냉각속도는 평형속도보다 빠르므로 변태온도가 그림 2.4에 나타낸 것과 같이 이동된다. 순철의 경우와 마찬가지로 급속가열시에 상승된 변태온도를 첨자 c를 붙여서 Ac1, Ac3 및 Accm 등으로 나타내고, 급속냉각시에 저하된 변태온도를 첨자 r을 붙여서 Ar1, Ar3 및 Arcm 등으로 나타낸다. 
그림 2.4. 탄소강의 가열 및 냉각시 변태점의 변화 : 가열 및 냉각속도는 0.125℃/min. |
● 탄소강의 서냉시 조직변화 여기서 서냉(徐冷)이라 함은 평형냉각에 가까운 냉각속도를 말하는 것으로서, 실제적인 열처리에서는 얻을 수도 없고, 또 큰 의미도 없는 냉각속도이지만 Fe-Fe3C 상태도를 통하여 평형냉각시의 미세조직변화를 이해시켜서 후술하는 연속냉각변태의 기초로서 응용할 수 있다는 데에 그 중요성은 매우 크다고 사료된다. |
◆ 공석강 0.8%C의 공석탄소강을 750℃ 정도로 가열하여 충분한 시간동안 유지하면 조직은 균일한 단상의 오스테나이트가 되는데, 이 과정을 오스테나이트化(austenitizing)라고 한다. 이 공석강을 평형에 가까운 냉각속도로 서냉시킬 때 그림 2.3에서 e로서 지시되는 온도, 즉 공석온도 직상에서는 아직까지 조직은 오스테나이트 상태로 있다. 그러나 온도가 더 내려가서 공석온도 이하로 되면(f점) 오스테나이트는 α페라이트와 시멘타이트(Fe3C)의 혼합조직으로 변태하게 된다. 이 조직은 페라이트와 시멘타이트가 교대로 반복되어지는 층상조직(層狀組織, lamellar structure)을 형성하고 있다. 이 조직은 광학현미경으로 나타낸 것으로서, 그 형태가 진주(pearl)와 비슷하기 때문에 펄라이트(pearlite)라고 불리워진다. 이와같이 펄라이트는 단상조직이 아니라 페라이트와 시멘타이트의 2상혼합조직이라는 사실에 유의해야 할 것이다. 따라서 서냉된 0.8%C의 공석강을 A1 변태온도 직하에서 지렛대법칙(lever rule)을 적용시키면 이 합금을 구성하고 있는 페라이트와 시멘타이트의 중량분율을 알 수 있다. 즉, 페라이트의 분율(wt%) =  시멘타이트의 분율(wt%) = 
따라서 723℃와 상온에서 페라이트의 탄소 고용도한계의 차이가 거의 없기 때문에 펄라이트 조직은 상온에서 약 88%의 페라이트와 12%의 시멘타이트로 구성되어 있게 되고, 또한 페라이트와 시멘타이트의 밀도가 거의 비슷하기 때문에 펄라이트 조직에 나타나는 페라이트와 시멘타이트의 면적비율은 약 7:1정도가 된다. |
◆ 아공석강 0.4%C의 아공석 탄소강을 900℃(그림 2.3의 a)로 가열하여 충분한 시간동안 유지하게 되면 공석탄소강에서와 마찬가지로 균일한 오스테나이트로 된다. 그리고는 이 아공석강을 그림 2.3의 b점(약 775℃)까지 서냉시키면 오스테나이트 결정립계에서 初析페라이트(proeutectoid ferrite)가 우선적으로 핵생성하기 시작한다. 이 강을 다시 c 점까지 서냉시키면 초석페라이트는 오스테나이트 속으로 계속해서 성장해간다. 이때 페라이트가 형성된 지역의 과잉탄소는 오스테나이트-페라이트 계면으로부터 오스테나이트 속으로 밀려나므로 남아있는 오스테나이트의 탄소량은 점점 많아지게 된다. 따라서 A1 변태온도 직상인 c 점에 도달되면 남아있는 오스테나이트의 탄소량은 0.4%에서 0.8%로 증가하게 된다. 한편 A1 변태온도인 723℃ 직하인 d 점에 도달되면 남아있는 오스테나이트는 공석반응에 의해서 펄라이트로 변태하게 된다. 펄라이트를 구성하고 있는 페라이트는 초석 페라이트와 구별하기 위해서 共析페라이트(eutectoid ferrite)라고 부르며, 이 두 페라이트의 조성은 평형조건하에서는 같아진다. A1 변태온도 직상인 c 점에서 지렛대법칙을 사용하면 초석 페라이트와 오스테나이트의 중량분율을 다음과 같이 계산할 수 있다. 초석 페라이트 분율 (wt%) =  오스테나이트 분율 (wt%) = 
723℃의 A1 변태온도에서 남아있는 모든 오스테나이트는 A1 변태온도 이하로 냉각될 때에 펄라이트로 변태하기 때문에, 그림 2.3에서 A1 변태온도 직하인 d 점에서의 펄라이트의 중량분율은 A1 변태온도 직상인 c 점에서의 오스테나이트의 중량분율과 같게 될 것이다. 따라서 0.4%C의 아공석강에 있어서 723℃ 직하의 온도에서 존재하는 펄라이트의 중량분율은 50%가 된다. 한편 A1 변태온도와 상온에서 페라이트의 탄소 고용도한계의 차이는 미미하므로 상온에서의 초석 페라이트와 펄라이트의 상대적인 양은 d 점에서 계산된 값과 비교해서 큰 차이가 없다. |
◆ 과공석강 과공석 탄소강을 서냉시킬 때 나타나는 초석상은 시멘타이트이다. 1.2%C의 과공석강을 950℃(그림 2.3의 g점)에서 오스테나이트화한 후에 냉각할 때에 나타나는 미세조직 변화과정을 살펴보기로 하자. 이 강이 그림 2.3의 h점의 온도로 서냉되면 오스테나이트 결정립계에서 初析시멘타이트(proeutectoid cementite)가 핵생성되어 성장하게 된다. 다시 이 강이 j점까지 냉각되는 동안에 초석시멘타이트는 계속 성장해 가면서 오스테나이트에 있는 탄소를 고갈시키게 된다. 이 냉각과정이 평형냉각이라고 가정할 때에 j점의 온도에서 남아있는 오스테나이트의 탄소량은 1.2%에서 0.8%로 감소하게 될 것이다. 따라서 이 오스테나이트는 A1 변태온도 이하로 냉각되면서 공석반응에 의한 펄라이트로 변태하게 된다. 펄라이트를 구성하고 있는 시멘타이트는 초석시멘타이트와 구별하기 위해서 共析시멘타이트(eutectoid cementite)라고 부른다. A1 변태온도 직상인 그림 2.3의 j점에서 지렛대법칙을 사용하면 초석시멘타이트와 오스테나이트의 중량분율을 구할 수가 있다. 즉, 초석시멘타이트 분율 (wt%) =  오스테나이트 분율 (wt%) = 
아공석강에서와 마찬가지로 공석온도인 723℃ 직상에서 남아있는 오스테나이트는 723℃ 이하로 냉각시 펄라이트로 변태하므로 그림 2.3에서 A1 변태온도 직하인 d 점에서의 펄라이트의 중량분율은 A1 변태온도 직상인 k점에서의 오스테나이트의 중량분율과 같게 될 것이다. 따라서 1.2%C의 과공석강에 있어서 723℃ 직하의 온도에서 존재하는 펄라이트의 중량분율은 93.2%가 된다. 한편 A1 변태온도와 상온에서 페라이트의 탄소 고용도한계의 차이는 미미하므로 상온에서의 초석시멘타이트와 펄라이트의 상대적인 양은 k점에서 계산된 값과 비교해서 큰 차이가 없다. 그림 2.7은 1.4%C의 과공석강을 970℃에서 오스테나이트화한 후 서냉(100℃/hr)한 조직을 보여주는 것으로서, 초석시멘타이트가 오스테나이트 결정립계를 따라서 망상으로 형성되어 있는 것을 볼 수 있다. 참고문헌 1. Heat Treating, in Metals Handbook, Vol.4, 9th Ed., American Society for Metals, Metals Park, Ohio, 1981 2. 歌川 寬 : やさしい 金屬熱處理技術の基礎, 啓學出版, 1981 3. G. Krauss : Principles of Heat Treatment of Steels, American Society for Metals, Metals Park, Ohio, 1980 4. C. R. Brooks : Heat Treatment of Ferrous Alloys, McGraw-Hill, New York, 1979 5. 日本熱處理技術協會 : 熱處理の基礎(Ⅰ), 日刊工業新聞社, 1970 6. C. R. Barrett, W. D. Nix, and A. S. Tetelman : The Principles of Engineering Materials, Prentice-Hall, New Jersey, 1973 7. L. E. Samuels : Optical Microscopy of Carbon Steels, American Society for Metals, Metals Park, Ohio, 1980 8. 金屬熱處理技術便覽編輯委員會 : 金屬熱處理技術便覽, 日刊工業新聞社, 1961 9. P. M. Unterweiser, H. E. Boyer, and J. J. Kubbs : Heat Treater's Guide, American Society for Metals, Metals Park, Ohio, 1982 10. 金文一 : 金屬組織學, 普文堂, 1993 |
■ 항온변태와 연속냉각변태 ● 항온변태 ◆ 항온변태곡선 공석강을 A1 변태온도 이상으로 가열한 후 어느정도의 시간을 유지하게 되면 단상의 오스테나이트가 되는데, 이와같이 오스테나이트화한 후에 A1 변태온도 이하의 어느 온도로 급랭시켜서 이 온도에서 시간이 지남에 따라 오스테나이트의 변태를 나타낸 곡선을 항온변태곡선(恒溫變態曲線, isothermal transformation curve)이라 하고, 다른 용어로는 TTT곡선(time-temperature-transformation curve), C곡선, 또는 S곡선이라고 불리어진다.

그림 3.1. 공석강의 항온변태곡선 그림 3.1은 공석강(0.8%C강)의 전형적인 항온변태곡선을 나타낸 것이다. 여기서 보면 항온변태곡선은 2개의 C자 형상을 가진 곡선으로 구성되어 있는데, 왼쪽 곡선은 변태개시선을, 오른쪽 곡선은 변태종료선을 나타내는 것이다. 또한 550℃ 부근의 온도에서 곡선이 왼쪽으로 돌출되어 있는데, 이것은 변태가 이 온도에서 가장 먼저 시작된다는 것을 의미하는 것으로서 이 곡선의 nose라고 부른다. 이와 같이 항온변태곡선의 중요한 특징은 변태가 시작되는 시간과 종료되는 시간을 나타낸다는 것으로서, 일반적으로 nose온도 위에서 항온변태시키면 펄라이트(pearlite)가 형성되고, nose 아래의 온도에서 항온변태시키면 베이나이트(bainite)가 형성된다. 펄라이트와 베이나이트 두 조직 모두 페라이트와 시멘타이트로 이루어져 있으나, 펄라이트는 두 상이 교대로 반복되어지는 층상조직을 나타내고 있고 베이나이트는 침상에 가까운 형태를 나타낸다. 또한 펄라이트 형성온도범위중 비교적 높은 온도에서 형성된 펄라이트는 조대하고, 비교적 낮은 온도에서 형성된 펄라이트는 미세하다. 베이나이트 역시 형성온도에 따라 조직의 차이를 보이는데, 350∼550℃범위의 온도에서 형성된 상부베이나이트(upper bainite)는 페라이트 주위에 시멘타이트가 석출되는 반면에, 250∼350℃ 온도범위에서 형성된 하부베이나이트(lower bainite)에서는 페라이트 내에 시멘타이트가 석출되어 있다. 한편 그림 3.2는 공석강과 아공석강의 항온변태곡선을 Fe-C 상태도와 관련시켜서 나타낸 것이다. 그림 3.2의 (b)에서 보면 펄라이트가 형성되기 시작하는 시간과 종료되는 시간은 nose 부근에서 가장 짧고, A1선으로 온도가 올라갈수록 시간이 오래 걸린다. 또 그림 3.2의 (c)에서 보면 아공석강인 0.5%C강에서는 또다른 곡선이 하나 존재하는데, 이것은 초석페라이트가 형성되기 시작하는 시간을 나타내는 곡선이다. 이와 비슷하게 과공석강에서도 초석시멘타이트가 형성되기 시작하는 곡선이 존재한다. 공석강과 아공석강의 항온변태곡선에서 나타나는 또 하나의 차이점은 마르텐사이트(martensite)가 형성되기 시작하는 온도인 Ms 온도가 다르다는 것이다. 일반적으로 탄소함량이 적을수록 Ms 온도는 올라간다. 
그림 3.2 Fe-C 상태도(a)와 공석강의 항온변태곡선(b) 및 0.5%탄소강의 항온변태곡선과(c)의 관계 |
◆ 펄라이트의 형성 공석강을 850℃로부터 750℃까지 냉각해서 이 온도에서 항온유지시키면 어떠한 변태도 일으키지 않는다. 그러나 650℃까지 냉각시켜서 항온유지하면 1초후에 펄라이트 변태가 시작되고 10초 이내에 변태가 완료된다(그림 3.3(a)의 곡선 II). 펄라이트 형성온도가 낮아짐에 따라 층상펄라이트는 점점 미세해지고 조직은 더욱 경화된다. 
그림 3.3 | -
(a) 0.80%C (b) 0.45%C (c) 1.0%C를 함유한 강에 대한 여러 가지 냉각프로그램으로부터 얻어지는 조직상의 상태 ; -
A=오스테나이트, B=베이나이트 C=시멘타이트 F=페라이트 -
P=펄라이트 M=마르텐사이트 Ms= 마르텐사이트 생성 개시온도
|
펄라이트 형성과정을 시멘타이트의 형성으로부터 시작된다고 가정하면, 오스테나이트에서 시멘타이트가 형성되기 위해서는 탄소원자가 확산이동해 와야만 하고, 동시에 시멘타이트의 인접한 지역은 탄소가 고갈되므로 페라이트가 형성되어, 시멘타이트와 페라이트층이 나란히 성장해간다. 공석강을 860℃에서 오스테나이트화 한 후 705℃에서 항온변태시킬 때 유지시간에 따른 조직의 변화를 보면, 소정의 잠복기(潛伏期, incubation period)가 지난 후에 생성된 펄라이트 콜로니(colony)의 핵이 이웃한 핵에서 성장하는 콜로니와 만날 때까지 계속 성장해간다. A1 변태온도 직하에서 핵생성속도는 작고 핵성장속도는 비교적 크기 때문에 단지 소수의 핵만이 형성되어 성장하게 된다. 그리고 이 온도에서 형성된 펄라이트의 층상간격(層狀間隔, interlamellar spacing)은 비교적 큰 편이다. 그림 3.3(b)에 있는 아공석강의 경우, 750℃에서 변태를 일으키면 페라이트만이 형성되어 페라이트와 오스테나이트의 2상 평형상태가 된다(곡선 I). 변태를 650℃에서 일어나게 하면 페라이트가 우선적으로 형성되고, 잠시후에 펄라이트가 형성된다. 그림 3.3(c)에 나타낸 과공석강의 경우에도 유사한 방법으로 시멘타이트가 우선적으로 형성되고, 그 다음에 펄라이트가 형성된다. |
◆ 베이나이트의 형성 공석강을 약 550℃이하의 온도에서 항온변태시키면 베이나이트가 형성되기 시작한다. 베이나이트의 형성은 오스테나이트 결정립계에서 페라이트 핵의 형성으로부터 시작된다고 가정하고 있다. 페라이트 핵이 형성되면 주위의 오스테나이트 탄소농도는 증가해서 시멘타이트가 형성되어, 페라이트와 시멘타이트가 나란히 성장해간다. 베이나이트는 형성온도에 따라 상부베이나이트와 하부베이나이트로 분류되는데, 공석강을 860℃에서 오스테나이트화 한 후 500℃에서 0.5초간 항온변태시킨 상부베이나이트조직을 보면 깃털모양의 상부베이나이트 조직과 일부 펄라이트가 나타나는 것을 알 수 있다. 일반적으로 상부베이나이트는 비교적 취약한 반면, 하부베이나이트는 비교적 인성을 가지고 있는 것으로 알려져 있다. 한편 비교적 낮은 온도인 300℃에서 형성된 하부베이나이트조직은 상부베이나이트와는 다른 형태를 나타낸다. 공석강을 860℃에서 오스테나이트화 한후 300℃에서 항온유지시간에 따른 조직의 변화를 보면 형태는 깃털모양이라기 보다는 침상의 형태를 보이고 있다. 공석강에서 상부베이나이트에서 하부베이나이트로의 천이는 350℃ 정도에서 일어나지만 그 경계를 명확히 구분하기는 어렵다. 그러나 상부베이나이트의 경도는 변태온도에 따라 약간 변화되는데 비하여 하부베이나이트의 경도는 변태온도가 저하함에 따라 급격히 증가된다. 또한 상부베이나이트는 동일경도로 퀜칭 템퍼링한 조직보다 인성이 그다지 높지 않지만, 하부베이나이트는 동일경도의 퀜칭 템퍼링한 조직보다 현저하게 큰 인성을 나타낸다. |
● 연속냉각변태(continuous cooling transformation) ◆ 공석강의 연속냉각변태 대부분의 실제 열처리작업에서는 항온변태에 의해서 강을 열처리하기도 하지만 오스테나이트 온도영역에서 상온까지 연속적으로 냉각변태시켜서 열처리하고 있는 경우도 많다. 따라서 항온변태곡선을 연속냉각변태곡선으로 전환시키지 않으면 안된다. 이를 위해서는 항온변태곡선 위에 연속냉각곡선을 그려서 구할 수가 있다. 세로축은 온도, 가로축은 시간(log 눈금)으로 정하여 항온변태곡선 위에 여러가지 냉각속도로 냉각시켰을 때의 연속냉각곡선을 그림 3.4에 나타냈는데, 여기서는 간단히 하기 위해서 냉각곡선을 직선으로 표시하였다. 前章에서 공석강, 아공석강 및 과공석강을 연속적으로 서냉시켰을 때의 조직변화에 대하여 자세히 알아보았는데, 이때에는 거의 평형냉각을 가정했기 때문에 그림 3.4의 도움없이도 Fe-Fe3C 상태도를 통하여 상변화를 예측할 수 있었다. 그러나 실제적인 열처리작업에서는 아무리 느린 냉각인 노냉(爐冷, furnace cooling)을 시킨다 해도 평형냉각보다는 매우 빠른 냉각이고, 더욱 빠른 냉각인 유냉(油冷, oil quenching)이나 수냉(水冷, water quenching)은 비평형냉각조건이 되기 때문에 Fe-Fe3C 상태도로부터 상변화를 예측할 수 없다. 따라서 그림 3.4를 통하여 연속냉각속도에 따른 변태조직의 변화에 대하여 기본적인 안목을 기르는 것이 특수강을 포함한 실제 열처리작업에 직접적으로 연결되기 때문에 후술하는 내용의 중요성은 재언을 요하지 않는다.

그림 3.4. S-곡선과 연속냉각곡선과의 관계 지금 몇개의 공석강 시험편을 A1 변태점 이상의 온도(그림 3.4에서 t)로 가열한 후, 여러 냉각속도(v1∼v6)로 냉각시켰다고 하자. 이때 그림 3.4에서 직선의 기울기가 클수록 냉각속도가 큰 것이다. 노냉과 같이 제일 느린 냉각은 직선 v1, 공랭처럼 약간 빠른 냉각은 직선 v2, 유냉과 같이 더욱 빠른 냉각은 v3, v4, 수냉과 같이 가장 빠른 냉각은 v5, v6로 나타내진다. 제일 느린 냉각속도인 v1에서는 냉각곡선이 펄라이트 변태의 개시 및 종료선을 통과하고 있다. 즉 변태개시선과는 a1점에서, 종료선과는 b1점에서 교차하고 있다. 이와 같이 노냉시에는 오스테나이트가 펄라이트로 변태하게 된다. 특히 이 변태가 변태개시선의 가장 높은 온도에서 일어나므로 이 펄라이트 조직은 조대하게 된다. 좀더 빠른 냉각속도(공랭)인 v2에서도 역시 냉각곡선이 펄라이트 변태의 개시 및 종료선을 통과하고 있으므로 오스테나이트는 펄라이트로 변태된다. 그러나 변태개시온도가 a2이고, 종료온도가 b2이므로 노냉시보다는 약간 낮기 때문에 펄라이트 조직은 좀더 미세해진다. 이와같이 공랭에 의해서 형성된 미세 펄라이트를 소르바이트(sorbite)라고 부른다. 더욱 빠른 냉각속도인 v3의 냉각속도에서는 변태온도가 더욱 낮으므로 형성된 펄라이트는 소르바이트보다 더욱 미세해진다. 이와 같이 가장 미세한 펄라이트를 트루스타이트(troostite)라고 부르며, 트루스타이트 변태가 시작되는 온도를 Ar'이라고 한다. 이와 같은 이유로 해서 v3보다 빠른 냉각일 경우에 냉각곡선은 단순히 변태개시선과 a4에서 교차될 뿐이며 종료선과는 교차되지 않는다. 이것은 펄라이트 변태가 시작되었을 뿐 종료되지 않았다는 것을 이미한다. 다시 말하면 일부의 오스테나이트는 펄라이트로 변태되지만 나머지는 펄라이트 조직으로 변태할 만한 시간적 여유가 없었다는 것을 나타내는 것이다. 따라서 펄라이트로 변태되지 못하고 남아 있는 오스테나이트는 그대로 냉각되다고 m4점에 도달되면 마르텐사이트로 변태하게 된다. 이와 같은 마르텐사이트 변태가 시작되는 온도를 Ar'', 또는 흔히 Ms점이라고 한다. 그러므로 v4의 속도로 냉각하면 트루스타이트와 마르텐사이트의 혼합조직을 얻을 수가 있고 이때의 냉각속도는 유냉에 해당된다. 냉각속도가 v5보다 클 때에는 오스테나이트는 전혀 페라이트와 시멘타이트로 분해되는 일 없이 모두 마르텐사이트로 변태된다. 탄소강에서는 이러한 냉각속도가 수냉에 해당된다. v3와 같이 펄라이트를 형성함이 없이 전적으로 마르텐사이트를 형성시키는 최소의 냉각속도를 임계냉각속도(臨界冷却速度, critical cooling rate)라고 한다. 그림 3.4에서 연속냉각변태를 설명할 때 주의해야 할 사항이 한가지 있다. 즉 그림에서 냉각속도 v3∼v1은 도면상에서 마르텐사이트 변태개시온도인 Ms점을 통과하고 있다. 예를 들면 냉각곡선 v3는 m3점에서 Ms선과 교차하고 있지만 마르텐사이트로 변태하는 것은 아니다. 왜냐하면 이 냉각곡선은 이미 펄라이트 변태개시선과 종료선을 통과했기 때문에 전부 펄라이트로 변태되어 마르텐사이트로 변태할 오스테나이트가 남아있지 않기 때문이다. 따라서 마르텐사이트 변태는 일어나지 않게 되고, m3점보다 오른쪽의 Ms선은 아무런 의미가 없는 선이 되는 것이다. |
◆ 연속냉각변태도 한편 공석탄소강을 연속냉각시키면 오스테나이트로부터 펄라이트로의 변태개시는 어느 일정한 온도에서 일어나는 것이 아니라 냉각속도가 커짐에 따라 변태개시온도는 낮아진다. 그러므로 그림 3.4에서와 같이 항온변태곡선으로부터 연속냉각에 의해서 형성되는 조직을 직접적으로 예측하는 것은 실제적으로 정확한 것이 아니다. 실험결과에 의하면 공석탄소강에서의 연속냉각변태도는 항온변태곡선에 비하여 좀더 저온측으로 그리고 좀더 장시간쪽으로 이동되어 있다는 사실을 알 수 있다. 일반적으로 항온변태곡선을 IT 곡선, 또는 TTT곡선이라고 부르는 것과 구별하기 위해서 연속냉각변태도를 CCT곡선(continuous cooling transformation diagram)이라고 부른다. 한편 공석강의 연속냉각변태도 위에 오스테나이트화 온도로부터 여러가지 속도로 냉각시켰을 때의 냉각곡선과 그에 따른 형성조직을 일반적으로 다음과 같이 구분한다. 매우 느린 냉각인 노냉에 의해서 조대한 펄라이트를 형성시키는 열처리 방법을 풀림(annealing)이라고 하고, 좀더 빠른 냉각인 공랭에 의해서 미세한 펄라이트인 소르바이트를 형성시키는 열처리방법을 노멀라이징(normalizing)이라고 한다. 또한 가장 급랭인 수냉에 의해서 전부 마르텐사이트 조직을 얻는 열처리방법을 퀜칭(quenching)이라고 하는데, 이 방법은 강을 경화시키는 열처리방법으로서 그 중요성이 매우 크다. 한편 곡선 C와 같은 냉각속도에서는 앞서 설명한 바와 같이 미세한 펄라이트의 변태가 개시되지만 이 변태를 완료시킬 만한 충분한 시간이 없기 때문에 펄라이트로 변태하지 못하고 남아있는 오스테나이트가 마르텐사이트로 변태하게 된다. 따라서 최종조직은 극히 미세한 펄라이트인 트루스타이트와 마르텐사이트의 혼합조직으로 된다. 공석탄소강의 연속냉각변태도로부터 알 수 있는 또하나의 중요한 사실은 펄라이트 변태를 일으키고 난 후에야 베이나이트 변태개시선이 통과된다는 것이다. 이 사실은 연속냉각에 의해서는 베이나이트 변태가 일어날 수 없다는 것을 의미한다. 따라서 베이나이트 조직을 얻기 위해서는 공석강을 Ms온도와 nose 온도사이로 급랭시켜서 항온변태시키는 수 밖에 없다. 그러나 이것은 탄소강에만 해당되는 것으로서 합금원소가 첨가된 특수강에서는 연속냉각에 의해서도 베이나이트 변태를 일으킬 수 있다. |
◆ 마르텐사이트 변태 오스테나이트 상태로부터 상온으로 급격히 냉각(퀜칭)하면 탄소가 확산할 만한 시간적 여유가 없으므로 이동하지 못하여 α철 내에 고용상태로 남아 있게 된다. 그런데 탄소원자가 차지할 수 있는 격자틈자리의 크기는 γ철(0.51Å)에서보다는 α철(0.35Å)에서 더 작기 때문에 격자가 팽창될 수밖에 없다. 이때 야기되는 응력 때문에 강의 경도가 증가되어 경화된다. 이와 같이 α철 내에 탄소가 과포화 상태로 고용된 조직을 마르텐사이트(martensite)라고 부른다. 이 마르텐사이트 변태가 시작되는 온도를 MS점, 종료되는 온도를 Mf점이라고 하며, 이 온도는 오스테나이트의 화학조성에 따라서 달라지는데 공석강에서는 약 230℃정도이다. 그밖에 탄소량에 따른 MS, Mf점의 변화를 보면, 탄소량이 증가됨에 따라 MS, Mf점은 저하하는 것을 알 수 있다. 또한 마르텐사이트 조직의 형태도 탄소량에 따라서 래스(lath), 혼합 및 판상(plate) 마르텐사이트로 변화된다. 한편 펄라이트와 베이나이트의 형성은 변태시간에 따라 진행되는 반면에, 마르텐사이트 형성은 변태시간에는 무관하고 Ms 온도 이하로의 온도강하량에 따라서만 결정된다. 일반적으로 공석강을 850℃에서 오스테나이트화 한 후 Ms온도 아래로 냉각시킴며 관찰한 따른 마르텐사이트 형성과정을 보면 210℃, 200℃, 180℃ 및 20℃로 온도가 내려감에 따라 마르텐사이트 변태량이 증가함을 명확히 알 수 있다. |
◆ 잔류오스테나이트 공석강을 퀜칭하면 오스테나이트가 100% 마르텐사이트로 변태하는 것이 아니라 일부의 오스테나이트가 마르텐사이트로 변태되지 못하고 상온까지 내려오게 된다. 이와 같이 상온에서 존재하는 미변태된 오스테나이트를 잔류오스테나이트(retained austenite)라고 한다. 그림 3.13에서 보는 바와 같이, 0.6%C 이상의 탄소강에서는 Mf온도가 상온이하로 내려가기 때문에 상온까지 퀜칭하여도 마르텐사이트 변태는 종료되지 않는다. 이것이 잔류오스테나이트를 형성시키는 이유로 된다. 한편 퀜칭한 강을 상온이하의 어느 온도로 냉각시키면 잔류오스테나이트가 마르텐사이트로 변태하게 되는데, 이와 같은 처리를 심랭처리(深冷處理, sub-zero treatment)라고 한다. 고탄소강이나 고합금강에서는 잔류오스테나이트가 많이 존재하므로 퀜칭경도가 낮아질 수 있다. 또한 잔류오스테나이트는 상온에서 불안정한 상이므로 이것이 존재하는 강을 상온에서 방치시 또는 사용시 마르텐사이트로 변태되어 치수변화를 일으키고, 연마시에도 마르텐사이트로 변태되어 균열을 일으킬 염려가 있다. 심랭처리에 사용되는 냉매로는 드라이아이스(-78℃)나 액체질소(-196℃) 등이 있는데, 이 심랭처리에 대해서는 다음에 자세히 서술하고자 한다. |
● 강의 변태에 미치는 합금원소의 영향 앞에서는 강에서 일어나는 펄라이트변태나 마르텐사이트변태 등에 대한 기본적인 사항을 설명하였다. 본절에서는 탄소강에 합금원소가 첨가되었을 때에 이러한 변태상황이 어떻게 달라지는지를 설명하고자 한다. 즉, 탄소강에 Ni 이나 Cr 등의 합금원소가 첨가되면 S곡선이 우측으로 이동하여 펄라이트 변태가 일어나기 어려워짐으로 두께가 큰 강재를 퀜칭할 때에 냉각속도가 작아도 마르텐사이트 조직을 얻을 수 있고, 또한 18Cr-8Ni 스테인리스강에서처럼 MS점이 현저하게 저하됨으로써 상온에서도 완전한 오스테나이트 조직상태로 존재하게 된다. 퀜칭-템퍼링 처리를 행하여 사용하는 기계구조용강이나 공구강에서 합금원소를 첨가하는 목적은 여러가지가 있지만 그중에서도 중요한 사항은 전술한 바와 같이 펄라이트 변태를 억제시켜서 퀜칭에 의한 마르텐사이트 조직을 얻기 쉽도록 하기 위한 것이다. 즉 경화능을 향상시키기 위한 것이다. 경화능에 대한 구체적인 설명은 후술하기로 하고, 본절에서는 우선 경화능에 대한 예비지식으로서 펄라이트 변태와 마르텐사이트 변태에 대한 합금원소의 영향에 대해서 설명하기로 한다. |
◆ 펄라이트 변태에 미치는 영향 (1) A1, A3 및 Acm 선의 변화 강을 퀜칭하거나 풀림처리할 경우에 우선 오스테나이트 상태의 온도로 가열할 필요가 있다. 탄소강에서는 A3 또는 Acm선 이상으로 가열하면 오스테나이트 단상으로 되지만, 합금원소가 첨가되면 이 A3 및Acm선의 온도가 달라지므로 합금강에서는 오스테나이트 조직으로 하기 위한 가열온도의 선정에 주의할 필요가 있다.

-
그림 3.5. 오스테나이트 영역에 미치는 Cr과 C의 효과. 점선은 탄소강과 오스테나이트 영역을 나타낸다. -
즉, 공석점은 철과 탄소만을 함유한 합금에서는 이동되지 않음을 나타낸다.
그림 3.5는 Cr 첨가에 따라 A3선과 Acm선이 변화되는 상태 즉 오스테나이트 상영역이 변화되는 상태를 나타낸 것으로서, Cr량이 증가함에 따라 723℃, 0.8%C에 해당되는 A1변태점이 저탄소쪽으로 그리고 고온측으로 이동함으로 오스테나이트 단상영역은 Cr량이 증가함에 따라 점점 좁아지게 된다. 따라서 오스테나이트화 하기 위해서는 보다 높은 온도로 가열해야만 한다는 것을 알 수 있다. 이와 같은 경향은 탄소와의 친화력이 강한 원소 즉 탄화물 형성원소에서 공통적으로 볼 수 있는 현상으로서, 예를 들면 0.8%C-18%W-4%Cr-1%V을 함유한 고속도공구강에서는 900℃ 정도로 가열시 오스테나이트 중에 고용되는 탄소량은 불과 0.25% 정도이므로 이것을 퀜칭하여 마르텐사이트 조직으로 변태시켜도 그다지 경화되지 못하지만, 1270∼1300℃로 가열하면 0.55% 정도의 탄소가 오스테나이트 중으로 고용됨으로 이것을 퀜칭하면 HRC 65∼67 정도의 경도를 얻을 수 있다.

그림 3.6. 공석온도와 공석탄소량에 미치는 첨가합금원소의 영향 여러가지 합금원소 첨가에 의한 A1 변태점과 공석탄소량의 변화를 그림 3.6에 나타냈는데, Ti, Mo, Si 및 W 등은 모두 A1 변태점을 상승시키고, 반대로 Ni과 Mn은 저하시킨다. 그림에 나타내지는 않았지만 질소도 A1 변태점을 저하시키므로 침탄질화에 의해서 질소가 鋼中에 들어가 있는 경우는 퀜칭온도를 다소 낮출 수 있다. 그림 ⒝는 공석탄소량의 변화를 나타낸 것으로서 여기에 나타낸 모든 원소가 공석탄소량을 낮춘다. 즉 Fe-Fe3C계에서 아공석(亞共析)의 탄소량에서도 이들 합금원소가 들어가면 공석(共析)이나 과공석(過共析)으로 되므로 전술한 바와 같이 탄화물을 완전히 고용시키는데에 보다 높은 온도가 필요하게 된다. (2) 펄라이트 변태속도의 변화 평형상태도상에서 A1 및 A3선이 합금원소 첨가에 의해서 변화되는 양상은 전술한 바와 같으나 실제로 오스테나이트 상태로부터 어느 냉각속도로 냉각시킬 때에 Ar3변태나 Ar1변태가 어떻게 나타나는가 하는 것은 냉각속도와 합금원소에 의해서 현저하게 달라진다. 펄라이트 변태속도는 핵생성속도(N)과 핵성장속도(G)에 의해서 결정되지만 합금원소중에서 Co와 Al만은 이 N과 G를 증가시켜서 펄라이트 변태를 촉진시키는 반면에 그 이외의 원소들은 펄라이트변태를 지연시키는 효과를 갖고 있다. 특히 Mo, Ni 및 Mn 등은 그 작용이 현저한데, 예를 들면 Mn은 0.2%에서 0.8%로 함유량이 증가하면 G를 1/5로 감소시키고, 또 Mo은 불과 0.5%첨가로서 G를 1/100로, N을 1/1000로 감소시킨다고 알려져 있다. 그림 3.7은 펄라이트 변태속도에 미치는 Ni의 첨가영향을 나타낸 것으로서, 오스테나이트 안정화원소(austenite stabilizer)인 Ni은 펄라이트변태를 지연시키기 때문에 펄라이트 변태개시선이 오른쪽으로 이동되어 있는 것을 볼 수 있다. 따라서 펄라이트 변태가 완료되는데에 걸리는 시간이 훨씬 길어지게 된다. 또한 Ni첨가에 의해서 A1 변태온도도 낮아짐을 알 수 있다.

그림 3.7. Austenite안정제 Ni에 의한 변태곡선의 이동. 이와같이 펄라이트변태를 지연시키는 합금원소를 첨가하면 두께가 큰 강재를 퀜칭하는 경우에 중심부의 냉각속도가 다소 늦더라도 펄라이트변태가 일어나기 어려우므로 완전한 마르텐사이트 조직으로 경화된다는 사실을 알 수 있다. |
◆ 마르텐사이트변태에 미치는 영향 (1) MS점과 합금원소 이미 서술한 바와 같이 마르텐사이트변태는 오스테나이트 상태로부터 급랭할 때 Ms온도에서 변태가 시작되고 일반적으로 그 이하로 온도강하량에 따라 변태량이 증가하다가 Mf온도에 도달하면 변태가 종료된다. Ms와 Mf사이의 온도구간은 보통 200∼300℃이다. 그러나 오스테나이트중의 탄소나 Ni함유량이 증가하면 MS점은 강하하므로 이들 원소량이 어느만큼 이상이 되면 상온에서 100% 마르텐사이트 조직을 얻을 수가 없다. 마르텐사이트 조직으로 변태시키는 것을 목적으로 하는 보통의 퀜칭에서는 우선 강종에 따라서 Ms점이 어떻게 다른가, 또 Ms점 이하로 온도가 내려감에 따라서 어떻게 마르텐사이트가 증가하는가를 알 필요가 있다. 강의 화학성분 중에서 Ms점에 가장 큰 영향을 주는 것은 탄소량이다. 이미 전술한 바와 같이 보통의 탄소강의 경우 탄소량 0.1% 증가에 따라 약 35℃정도 Ms점이 강하한다. 또한 Mf점은 탄소량에 따라 Ms점 이상으로 현저하게 강하되어 0.6% 이상의 탄소를 함유하는 강에서는 상온에서 오스테나이트의 일부가 잔류하게 된다. 탄소 이외의 합금원소로서는 Co와 Al만이 Ms점을 상승시키고 그밖의 실용원소는 거의 모두 Ms점을 강하시키는 작용을 하고 있다. 그림 3.8과 3.9는 여러가지 탄소량의 강에 Cr과 Mn을 첨가한 경우 Ms점의 변화를 나타낸 것으로서, Cr은 1% 첨가당 20℃정도, Mn은 탄소량에 따라 다소 차이나지만 1% 첨가당 약 40℃정도 Ms점을 강하시킨다.

그림 3.8. 강의 Ms점에 대한 Cr의 영향 
그림 3.9. 강의 Ms점에 대한Mn의 영향 이와같이 여러가지 합금원소가 강의 Ms점에 미치는 영향을 조사한 연구결과를 기초로 하여 강의 Ms점을 화학조성으로부터 계산할 수 있게 한 실험식이 몇가지 제안되고 있다. 그 一例는 다음과 같다. Ms(℃) = 550-350×C%-40×Mn%-35×V%-20×Cr%-17×Ni%-10×Cu%-10×Mo%-10×W%-10×Si%+15×Co% 위의 식에서 알 수 있듯이 탄소 다음으로 Mn, Cr, Ni순으로 Ms점의 강하효과가 약해지고, Si, W, Mo 등은 거의 같은 정도의 효과를 나타냄을 알 수 있으며, Co는 반대로 Ms점을 상승시킨다. 식 중에 포함되어 있지는 않지만 Al도 역시 Ms점을 상승시키지만 그 효과는 Co보다는 약하다. 또 Cu는 Ms점을 약간 저하시킨다고 알려져 있다. 그러나 위의 계산식은 함유원소가 전부 오스테나이트 중에 고용된 상태에서 퀜칭한 경우에만 적용되는 것이며, 탄화물 등의 고용이 완전치 못해서 일부분 잔류할 경우에는 오스테나이트 중의 고용원소량이 적어지므로 실제 MS점은 위의 식에서 계산된 Ms점보다 높아진다는데에 주의하여야 한다.

그림 3.10. 4종류의 1.1%C를 함유한 강에서 Ms점에 미치는 오스테나이트화 온도의 영향 그림 3.10은 1.1%C가 함유된 A강과 1.1%C에 1.5%Cr을 함유하는 B강, 2.8%Cr을 함유하는 C강 및 5.4%Ni을 함유하는 D강의 4강종에 대하여 오스테나이트화 온도에 따른 Ms점의 변화를 나타낸 것으로서, 탄소강과 Ni강에서는 850℃ 이상에서 이미 Fe3C가 완전히 고용되어 있으므로 Ms점의 변화는 적지만 Cr강에서는 퀜칭온도의 상승과 함께 시멘타이트나 Cr탄화물들이 오스테나이트 속에 고용되므로 Ms점은 현저히 저하된다. 이것으로부터 알 수 있듯이 공구강과 같이 탄화물이 잔류된 상태에서 퀜칭할 때에는 강전체의 화학성분을 알고 있더라도 Ms점을 계산할 수는 없다. 이 경우에 Ms점을 계산하기 위해서는 오스테나이트 자체의 화학조성을 알 필요가 있다. (2) 응력에 의한 잔류오스테나이트의 마르텐사이트화 오스테나이트는 외부로부터의 탄성적 혹은 소성적인 힘을 가함으로써 마르텐사이트변태를 일으킬 수가 있다. 18-8스텐레스강의 박판(薄板)이나 세선(細線)을 상온에서 압연하거나 인발하면 강한 자성을 나타내므로 마르텐사이트로 변태되었다는 것을 알 수 있다. 통상적인 퀜칭강에서도 오스테나이트가 잔류되어 있는 경우 여러가지 이유로 인하여 마르텐사이트로 변태된다. 해머로 쳐도 마르텐사이트로 변태할 때가 있고, 또 퀜칭한 충격시험편을 Charpy 충격시험기로 파단시키면 그 파단면으로부터 먼 부위에서는 잔류오스테나이트가 존재하지만 파단면 부근에서는 전부 마르텐사이트로 변태되어 있는 경우도 같은 현상으로 설명할 수 있다. 특히 퀜칭된 부품을 그라인더로 연삭하는 경우에 종종 발생되는 연삭균열은 부품의 일부가 연삭될 때 발생되는 열에 의해서 그 부품내부의 잔류응력분포가 변하고, 잔류오스테나이트가 국부적으로 마르텐사이트로 변태했기 때문인 것으로 생각된다. 이와 같이 잔류오스테나이트는 매우 불안정한 상이므로 상온에서 장시간 방치함에 의해서도 응력분포가 점차로 변화됨에 따라서 마르텐사이트로 변태하여 치수변화를 일으키거나 균열의 원인이 되기도 하므로 주의해야 한다. 참고문헌 1. G. Krauss and J. F. Libsch : Phase Diagrams in Ceramic, Glass and Metal Technology, A. M. Alper(Ed.), Academic Press, New York, 1970 2. 延倫模, 池武晟, 宋鍵, 洪英煥 : 金屬材料, 機電硏究社, 1994 3. 歌川 寬 : やさしい 金屬熱處理技術の基礎, 啓學出版, 1981 4. G. Krauss : Principles of Heat Treatment of Steels, American Society for Metals, Metals Park, Ohio, 1980 5. C. R. Brooks : Heat Treatment of Ferrous Alloys, McGraw-Hill, New York, 1979 6. 日本熱處理技術協會 : 熱處理の基礎(Ⅰ), 日刊工業新聞社, 1970 7. C. R. Barrett, W. D. Nix, and A. S. Tetelman : The Principles of Engineering Materials, Prentice-Hall, New Jersey, 1973 8. L. E. Samuels : Optical Microscopy of Carbon Steels, American Society for Metals, Metals Park, Ohio, 1980 9. 金屬熱處理技術便覽編輯委員會 : 金屬熱處理技術便覽, 日刊工業新聞社, 1961 10. P. M. Unterweiser, H. E. Boyer, and J. J. Kubbs : Heat Treater's Guide, American Society for Metals, Metals Park, Ohio, 1982 11. 金文一 : 金屬組織學, 普文堂, 1993 12. Atlas of Isothermal Transformation and Cooling Transformation Diagrams, American Society for Metals, Metals Park, Oh., 1977 |
■ 열처리방법 열처리방법을 크게 구분하면 주조나 단조후의 편석 및 잔류응력 등을 제거하여 균질화시키거나 또는 軟化를 목적으로 행하는 풀림(annealing), 결정립을 미세화하여 기계적성질이나 피삭성을 향상시키기 위한 노멀라이징(normalizing), 경화를 위하여 행하는 퀜칭(quenching), 그리고 강인화를 위한 템퍼링(tempering) 처리 등으로 나눌 수 있다. 또 표면은 내마모성이 크고, 중심부는 내충격성이 큰 이중조직을 나타내게 하는 표면경화(表面硬化, surface hardening)방법도 있다. |
● 평형상태도와 열처리 앞장에서 나타낸 그림 2.1은 Fe-Fe3C 상태도로서, 강을 매우 서서히 가열 및 냉각할 때의 조직변화, 즉 다시 말하면 풀림처리시의 조직변화를 나타낸 것이다. 그런데 열처리하기 위해서는 기본적으로 어느 온도범위로 가열할 필요가 있다. 여기서 우리는 강의 종류에 따라서, 또 열처리방법에 따라서 과연 가열온도는 어떻게 결정할 것인가 하는 의문을 제기할 수 있다. KS규격에 탄소공구강으로 규정된 STC 5강(0.8%C)을 퀜칭하고자 할 때에는 760∼820℃의 온도범위로 가열 후 수냉, 또 기계구조용 탄소강인 SM 45C(0.45%C)는 820∼870℃의 온도범위로 가열한 후에 수냉하는 것으로 규정되어 있다. 이들 온도는 그림 4.1에서와 같이 철-탄소계 평형상태도에 기초하여 A3 또는 A1 변태점 이상의 일정온도범위로 정해지는 것이다. 또 노멀라이징 온도범위도 A3 또는 Acm변태점으로부터 그림 4.2와 같이 결정되는 것이다. 이와 같이 철-탄소계 평형상태도는 강을 열처리할 때 가열온도를 결정하는 중요한 근거가 된다. 한편 탄소강의 풀림(노냉)과 같은 실제열처리시에는 물론이고, 노멀라이징(공랭)과 같은 실제열처리시의 조직변화도 Fe-Fe3C 상태도로부터 어느정도 예측이 가능하지만, 퀜칭열처리(수냉)시에는 냉각속도가 빠르기 때문에 평형상태도로부터 조직변화를 알 수 없다. 즉 냉각속도가 빠를 때에는 비평형상태로 되기 때문이다. 이 때에는 3장에서 나타낸 연속냉각변태도로부터 조직변화를 예측할 수밖에 없다. 
그림 4.1. 탄소강의 퀜칭온도 범위 
그림 4.2. 탄소강의 노멀라이징 온도범위 |
● 열처리방법 ◆ 풀림 기본적으로 軟化를 목적으로 행하는 열처리로서, 일반적으로 적당한 온도까지 가열한 다음 그 온도에서 유지한 후 서냉하는 조작을 말한다. 그밖의 처리목적으로는 내부응력의 제거, 절삭성 향상, 냉간가공성 향상 등을 통하여 기계적성질을 개선하기 위한 것이다. 풀림에는 완전풀림, 항온풀림, 구상화풀림, 응력제거풀림, 연화풀림, 확산풀림, 저온풀림 및 중간풀림 등의 여러 종류가 있다. 그림 4.3.은 여러가지 풀림처리시 처리온도범위를 나타낸 것이다. 
그림 4.3 각종 풀림 온도 범위 (1) 완전풀림(full annealing) 완전풀림은 아공석강에서는 Ac3점 이상, 과공석강에서는 Ac1점 이상의 온도로 가열하고, 그 온도에서 충분한 시간동안 유지하여 오스테나이트 단상 또는 오스테나이트와 탄화물의 공존조직으로 한 다음, 아주 서서히 냉각시켜서 연화시키는 조작방법으로서 일반적으로 풀림이라고 하면 완전풀림을 의미한다. 따라서 이 경우의 조직은 아공석강에서는 페라이트와 펄라이트, 과공석강에서는 망상 시멘타이트와 조대한 펄라이트로 된다. 일반적으로 열간압연 또는 단조작업을 행한 강재는 조직이 불균일하다든지, 잔류응력이 존재한다든지 또는 연화가 불충분하여 절삭가공이나 소성가공이 곤란할 때가 많다. 이 경우 금속재료를 연화시켜서 절삭가공을 쉽게하기 위해서는 완전풀림을 한다. 이와 같은 처리는 탄소량이 약 0.6% 이하인 기계구조용강에 적용되며, 탄소량이 이것보다 많은 공구강에서는 구상화풀림이 적합하다. 완전풀림의 가열온도는 아공석강에서는 Ac3점 이상 30∼50℃, 과공석강에서는 Ac1점 이상 약 50℃ 높은 온도가 적당하며, 너무 높은 온도에서 가열하면 결정립이 조대화되므로 주의하여야 한다. 그림 4.4는 고속도공구강의 완전풀림방법을 나타낸 것으로서, 특히 한번 퀜칭후 다시 퀜칭을 반복할 때에는 필히 중간에 풀림처리를 해야만 한다. 이 공정을 생략하면 결정립이 조대해져서 극히 취약해지기 때문이다. 
그림 4.4. 고속도강의 풀림곡선 (2) 항온풀림(isothermal annealing) 완전풀림의 일종으로서 단지 항온변태를 이용한다는 차이만 있을 뿐이다. 즉 완전풀림은 강을 오스테나이트화한 다음 서서히 연속적으로 냉각해서 강을 연화시키는 것인데 비하여, 항온풀림은 강을 오스테나이트화 한 후 TTT곡선의 nose온도에 해당되는 600∼650℃의 로속에 넣어 이 온도에서 5∼6시간 동안 유지한 다음 꺼내어 공랭하는 것이다. 그림 4.5는 일반적인 항온풀림과 완전풀림의 처리곡선을 비교하여 나타낸 것이다.

그림 4.5. 항온풀림과 완전풀림의 비교 고속도강과 같은 합금강은 아주 서냉하지 않으면 페라이트 변태가 끝나지 않으며, 잔류오스테나이트는 베이나이트나 마르텐사이트로 변태하므로 충분히 연화시킬 수 없게 된다. 그러나 이와 같은 합금강도 어느 일정한 온도에서 유지시켜 항온 변태를 시키면 단시간 내에 변태가 끝나므로 쉽게 연화된다. 항온풀림은 자동차부품용의 기계구조용 저합금강 뿐만 아니라 합금공구강 및 고속도공구강과 같이 합금원소를 많이 함유하는 공구강에서 풀림시간을 단축시키기 위해서 현장에서 흔히 이용된다.
(3) 확산풀림(diffusion annealing) 일반적으로 응고된 주조조직에서 주형에 접한 부분은 합금원소나 불순물이 극히 적고, 주형 벽에 수직한 방향으로 응고가 진행됨에 따라 합금원소와 불순물이 많아지며, 최후로 응고한 부분에 합금원소가 가장 많이 잔존하게 된다. 이와 같은 현상을 편석(遍析, segregation)이라 한다. 강괴의 경우, 편석은 1300℃정도에서 수시간 동안 가열하는 균질화 처리와, 그 다음의 열간가공에 의해서 어느 정도 균질화되지만 완전히 해소되지는 못한다. 따라서 이러한 상태의 주괴를 단조나 압연을 하면 편석된 것들이 가공방향으로 늘어나 섬유상 편석이 나타난다.인(P), 몰리브덴(Mo) 등이 많이 함유된 강에서는 그 경향이 더욱 두드러지게 나타난다. 이와 같은 주괴 편석이나 섬유상 편석을 없애고 강을 균질화시키기 위해서는 고온에서 장시간 가열하여 확산시킬 필요가 있다. 이와 같은 열처리를 확산풀림 또는 균질화풀림이라고 한다. 가열온도는 합금의 종류나 편석 정도에 따라서 다르며, 주괴편석 제거를 위해서는 1200∼1300℃, 고탄소강에서는 1100∼1200℃, 단조나 압연재의 섬유상 편석을 제거하기 위해서는 900∼1200℃ 범위에서 열처리하는 것이 적당하다. 확산풀림을 할 때 풀림온도가 높을수록 균질화는 빠르게 일어나지만 결정립이 조대화되므로 주의하여야 한다. (4) 구상화풀림(spheroidizing annealing) 펄라이트를 구성하는 층상시멘타이트나 또는 망상(網狀)으로 나타나는 초석시멘타이트가 그대로 존재하면 기계가공성이 나빠지고, 특히 퀜칭열처리시 균열이나 변형발생을 초래하기 쉬워진다. 즉 소성가공이나 절삭가공을 쉽게 하기 위해서, 기계적성질을 개선하기 위해서, 또는 퀜칭시 균열이나 변형발생을 방지할 목적으로 탄화물을 구상화시키는 열처리를 구상화풀림이라고 한다. 이 구상화처리는 보통 제강회사에서 실시하는 것이 일반적이다. 이 처리는 특히 공구강에서는 매우 중요한 처리로서, 퀜칭의 전처리로서 탄화물을 필히 구상화시킬 필요가 있다. 시멘타이트가 구상화되면 단단한 시멘타이트에 의하여 차단된 연한 페라이트 조직이 상호 연속적으로 연결되고, 특히 가열시간이 길어짐에 따라 구상 시멘타이트는 서로 응집하여 입자수가 적어지므로 페라이트의 연속성은 더욱 좋아진다. 따라서 경도는 저하되고 소성가공이나 절삭가공이 용이해진다. 즉, 구상화 풀림에 의해 과공석강은 절삭성이 향상되고, 아공석강에서는 냉간단조성 등의 소성가공성이 좋아지게 되는 것이다. 그림 4.8은 열처리조직에 따른 피삭성의 차이를 나타낸 것이다.

그림 4.6. 열처리 조직에 따른 피삭성 또한 전술한 바와 같이 공구강 등에서는 탄화물을 구상화시킴으로써 퀜칭경화 후 인성을 증가시키며, 퀜칭균열 방지효과도 있다. 구상화풀림 방법에는 그림 4.7과 같은 4가지가 주를 이루고 있다. 
그림 4.7. 탄화물의 구상화처리방법 1) 구상화방법 ① Ac1점 직상으로 가열한 후 Ar1점 이하까지 극히 서서히 냉각하든지 또는 Ar1점 이상의 어느 일정온도에서 유지한 후 냉각하는 방법. 탄소공구강은 처리가 간단하고 구상화속도도 비교적 빠르므로 이 방법으로 구상화시킨다. 그림 4.8은 탄소공구강의 구상화풀림곡선을 나타낸 것이다. 이 두방법중 일반적으로 사용되는 것은 서냉법(徐冷法)이고, 이 방법의 변화된 형태로서 항온유지법(恒溫維持法)이 이용되고 있다. 서냉법에서의 냉각속도는 보통 30℃/h 이하로 되어 있지만 각각 강종에 따라서 어느 임계냉각속도가 있어서 이 속도보다 빠르게 냉각하면 층상조직이 나타나게 된다. 
그림 4.8. 탄소공구강의 구상화풀림 ② Ac1점 직하(650∼720℃)에서 장시간 가열유지하는 방법. 주로 퀜칭 또는 냉간가공된 강에 적용된다. 아공석강에서도 냉간가공을 30% 이상 행한 경우는 이 방법으로 구상화시킨다. 이 방법으로는 조대한 망상 시멘타이트는 구상화되지 않는다. ③ Ac1점 상하 20∼30℃ 사이에서 반복적으로 가열 및 냉각하는 방법. 아공석강에 가장 적합한 방법으로서, 가장 빨리 구상화시킬 수 있다. 탄화물을 A1점 이상의 온도에서 고용시키면 탄화물의 부분적인 고용이 진행되고, 이에 따라 층상탄화물이 분단된다. 그리고 고용된 부분은 냉각시 재차 잔류탄화물의 표면에 석출하여 더욱 구상화가 촉진된다. 아공석강에서는 가열온도가 높아지면탄화물의 석출핵이 소실되어 구상화가 어려워진다. 냉각속도는 느린 편이 좋은데, 저탄소강에서는 1℃/min가 바람직하지만 탄소량이 많아지면 비교적 빠른 냉각으로도 구상화된다. 반복횟수는 아공석강 및 공석강에서는 3회, 과공석강에서는 2회 정도면 균일한 탄화물조직으로 된다. ④ Acm선 이상으로 가열하여 시멘타이트를 완전히 고용시킨 후 급랭하여 망상시멘타이트의 석출을 억제시키고 재차 가열하여 ② 또는 ③의 방법으로 구상화하는 방법. 망상 탄화물이 존재하는 과공석강의 구상화방법이다. 미세하고 균일한 구상화조직을 얻는데에는 효과적이지만 구상화속도가 느리다. 급랭으로는 주로 공랭을 이용하지만 마르텐사이트 조직이 가장 구상화되기 쉬우므로 유냉하는 경우도 있다. 2) 강종에 따른 구상화풀림 ① 냉간단조소재 : 냉간단조를 행한 아공석강에서는 구상화풀림이 매우 널리 이용되고 있다. 탄화물의 분포를 균일하게 하기 위해서는 전처리로서 노멀라이징을 행하여 초석페라이트와 펄라이트의 혼합조직으로 미세하게 해 놓는 것이 일반적이다. ② 탄소공구강과 합금공구강 : 절삭용, 내충격용 및 냉간금형용 공구강은 탄소공구강과 동일하지만 가열유지시간은 좀더 길고, 냉각은 좀더 신중하게 행한다. ③ 열간다이스강, 고속도강 : 공정탄화물이 있는 경우는 단조와 압연을 조합하여 행하고 있지만 이것은 통상 제강회사에서 행하여 공급하고 있다. ④ 베어링강 : 구상화조직은 베어링의 성능에 직접적으로 영향을 주므로 구상화풀림조건은 매우 엄격하게 되어 있다. 즉 1차 탄화물이 잔류하지 말아야 하고 탄화물분포가 균일해야 하며 그 입자크기도 0.4∼0.5㎛의 범위로 조절하고 있다. 구상화풀림 전에는 일반적으로 노멀라이징을 행하고, 풀림온도는 상한온도를 절대로 넘어서면 안된다. (5) 응력제거풀림(stress relief annealing) 단조, 주조, 기계가공 및 용접 등에 의해서 생긴 잔류응력을 제거시키기 위해서 A1점 이하의 적당한 온도에서 가열하는 열처리를 응력제거풀림이라고 한다. 잔류응력이 남아 있는 금속 부품을 그대로 사용하면 시간이 경과함에 따라 차차 그 응력이 완화되어 치수나 모양이 변화될 경우가 있다. 또 기계가공으로 어느 한 부분을 제거하면 물체 내부의 응력이 평형을 유지할 수 없게 되어 새로운 응력 평형 상태로 변화되므로 변형이 나타나게 될 경우가 많다. 이와 같은 변형을 방지하기 위해서는 재료를 적당한 온도로 가열하여 잔류응력을 충분히 제거해 줄 필요가 있다. 통상 재결정온도(450℃) 이상 A1 변태점 이하에서 행한다. 이 온도에서 두께 25㎜당 1시간 유지하고, 두께 25㎜당 200℃/h로 서냉시킨다. 일반적으로 가열온도가 높아질수록 재료는 연해지고, 잔류응력에 의해 소성변형이 일어나므로 응력이 완화제거된다. 일반적으로 탄소량이 많은 강일수록 잔류응력이 많고, 또 제거하기가 어렵다. 잔류응력제거와 함께 결정립의 미세화나 조직의 조절도 동시에 하고자 할 경우에는 완전풀림이나 노멀라이징을 한다. (6) 연화풀림(softening annealing) 대부분의 금속 및 합금은 냉간가공을 하면 가공경화에 의하여 강도가 증가되고 취약해져서 이 때문에 어느 가공도 이상으로 가공할 수 없게 된다. 특히 강에서는 탄소량이 많을수록 가공경화도가 커진다. 이렇게 경화된 것을 절삭가공을 한다든지, 또는 더 많은 냉간가공을 하고자 할 때에는 강을 일단 연화시킬 필요가 있다. 이를 위해서는 적당한 온도로 가열하여 가공조직을 완전히 회복시키거나 재결정 및 결정립 성장을 시켜야 한다.

그림 4.9. 냉간가공재의 가열에 의한 성질변화 냉간가공재를 가열할 경우의 조직과 성질의 변화를 그림 4.9에 나타내었다. 그림 4.9에서 보는 바와 같이, 연화과정은 3단계로 이루어진다. 즉 가열온도의 상승과 함께 회복, 재결정 및 결정립성장의 과정으로 변화된다. 첫단계인 회복은 가공에 의해서 증가된 전위밀도 감소와 전위의 재배열로 인한 연화이고, 재결정은 변형된 입자 속에서 변형되지 않은 새로운 결정입자로 대체하는 과정이며, 온도가 더욱 높아지면 미세한 입자가 응집, 조대화되는 결정립성장 단계로 된다. 이러한 변화는 내부에너지를 감소시킴으로써 보다 안정한 상태로 가고자 하는 현상 때문이며, 이러한 내부응력의 감소에 의해서 연화되는 것이다. 이와 같이 재결정에 의해서 경도를 균일하게 저하시킴으로써 소성가공 또는 절삭가공을 쉽게 하기 위한 풀림을 연화풀림이라고 하는데, A1점 위 또는 아래의 온도에서 가열한다. |
◆ 노멀라이징(normalizing) - (1) 목적
노멀라이징의 일반적인 목적은 다음과 같다. ① 결정립을 미세화시켜서 어느 정도의 강도증가를 꾀하고, 퀜칭이나 완전풀림을 위한 재가열시에 균일한 오스테나이트 상태로 만들어주기 위한 것이다. ② 주조품이나 단조품에 존재하는 편석을 제거시켜서 균일한 조직을 만들기 위함이다.
1) 단강품 단강품은 대부분 저탄소 또는 중탄소강으로서 열간가공온도나 살두께가 불균일하기 때문에 결정립의 크기가 불균일하고, 성장하여 조대해질 경우가 많다. 이러한 경우에 재차 오스테나이트화 한 다음 공랭하면 가공 등에 의한 잔류응력이 제거될 뿐만 아니라 결정립이 미세화된다. 이로써 강도와 인성이 증가된다. 단강품은 일반적으로 반드시 노멀라이징 또는 풀림을 하고 사용하여야 하며, 강도를 필요로 할 경우에 노멀라이징만으로도 상당한 효과를 얻을 수 있다. 단, 가열온도가 너무 높으면 결정립은 재차 성장하고 강도와 인성도 저하되므로 주의해야 한다. 2) 주강품 주강품에서는 응고시의 편석이나 서냉에 의한 결정립 조대화를 피할 수 없으며, 단면치수가 큰 것일수록 그 경향이 현저하다. 특히 편석이 심할 경우에는 노멀라이징 온도를 높이고 유지시간도 길게 하여 우선 확산, 균질화시킨 다음 공랭시키고, 재차 A3 변태점 직상으로 가열하여 새로운 미세한 오스테나이트를 형성시킨 다음 공랭하면 미세한 펄라이트가 생성된다. (2) 방법 강을 A3 또는 Acm점보다 30∼50℃ 정도 높은 온도로 가열하여 균일한 오스테나이트 조직으로 만든 다음 대기중에서 냉각하는 열처리이다. 가열시간은 25㎜당 30분이다. 이러한 통상적인 노멀라이징 방법 외에 다음과 같은 2가지 방법이 있다.
- ① 2단 노멀라이징 : 대형부품(두께 75㎜ 이상)이나 고탄소강(0.6∼1.0C)의 백점이나 내부균열을 방지하기 위하여 사용된다.
② 항온 노멀라이징 : 기계구조용 탄소강이나 저탄소 합금강의 피삭성을 향상시키기 위하여 사용된다. 그림 4.14는 3가지 노멀라이징 처리곡선을 나타낸 것이다.

그림 4.10. 노멀라이징의 3가지 방법 |
◆ 퀜칭 일반적으로 사용하는 "열처리"란 말은 주로 이 「퀜칭」을 의미한다고 해도 과언이 아닐 정도로 퀜칭은 열처리의 대명사처럼 여겨져 왔다. 즉 강을 軟한 상태로부터 가장 硬한 상태로 급격하게 변화시킴으로써 열처리효과를 가장 실감나게 해주는 방법이다. (1) 퀜칭의 목적 강의 퀜칭(quenching)은 오스테나이트화 온도로부터 급랭하여 마르텐사이트 조직으로 변태시켜서 강을 경화하는 열처리방법을 말하는데, 그 목적은 강의 종류에 의해 2가지로 대별된다. 그 하나는 공구강의 경우인데, 이것은 다른 금속재료를 절삭가공하기 위해 되도록 단단하거나 내마모성이 커야 하므로 고탄소 마르텐사이트의 특징인 큰 경도를 그대로 이용한다. 따라서 많은 공구강에서는 템퍼링온도를 150∼200℃의 비교적 낮은 온도로 하거나, 고합금강에서처럼 500∼600℃로 템퍼링을 하더라도 퀜징상태와 거의 같든지 혹은 그 이상의 경도가 얻어지도록 하여야 한다. 다른 하나의 경우는 구조용강으로서, 여기에는 강도도 요구되지만 오히려 강한 인성이 요구되는 용도로 제공하기 위해 일단 퀜칭해서 마르텐사이트 조직으로 하고, 500∼700℃의 상당히 높은 온도로 템퍼링을 해서 퀜칭상태에 비해 훨씬 낮은 경도 강도의 상태로 만드는 것이다. 예를 들면 기계구조용 탄소강에서 퀜칭상태의 인장강도는 170kg/mm2 이상이고, 브리넬경도도 500 이상이지만 실제로 사용될 때에는 충분한 템퍼링을 해서 인장강도 100kg/mm2 이하, 브리넬경도 300 이하로 한다. 그렇게 볼 때 무리하게 퀜칭할 필요없이 노멀라이징 정도면 되지 않겠는가 하는 의문이 생기나, 사실은 이와 같이 퀜칭과 템퍼링을 한 강은 노멀라이징 처리한 강에 비해 강도와 인성의 면에서 현저하게 우수하다.

그림 4.11. 기계구조용 탄소강의 노멀라이징재와 퀜칭, 템퍼링재의 기계적성질의 비교 그림 4.11은 기계구조용 탄소강 SM 30C, SM 40C 및 SM 50C를 노멀라이징 처리만 한 것과 퀜칭 템퍼링처리한 것의 강도와 인성을 비교한 것으로서, 퀜칭 템퍼링재의 노멀라이징재에 비해 충격치가 인장강도 60kg/mm2 급에서 약 2배 크고, 80kg/mm2 급에서는 약 4배를 나타내어 강인성에서 훨씬 우수하다는 것을 알게 된다. 또한 표 4.1에 나타낸 것처럼 Ni-Cr-Mo강의 퀜칭방법을 변화시켜서 마르텐사이트, 마르텐사이트와 베이나이트, 마르텐사이트와 펄라이트의 3종류의 조직으로 해서 인장강도가 약 89kg/mm2의 일정값이 되도록 각기 적당한 온도를 골라서 템퍼링처리를 했을 때의 충격값과 시험온도의 관계를 그림 4.12에 나타냈다. 그림에서 알 수 있듯이 완전 마르텐사이트조직을 템퍼링한 경우에 비해 베이나이트나 펄라이트를 갖는 불완전 퀜칭조직을 템퍼링한 것은 천이온도가 상승하여 상온이하에서의 충격값의 감소가 특히 심하다. 표 4.1 불완전 퀜칭에 의한 인성의 저하 

그림 4.12. 열처리 조직에 의한 충격값의 천이곡선의 변화 (2) 오스테나이트화
강을 퀜칭해서 마르텐사이트 조직으로 변태시키기 위해서는 우선 그 강을 오스테나이트 상태로 가열하여야 한다. 이 처리를 오스테나이트화라고 하며, 일반적으로 열처리시 냉각도중에 일어나는 모든 변태는 오스테나이트로부터 시작된다. 따라서 오스테나이트를 모상(母相, parent phase)이라고도 불리어진다. ① 가열온도 전술한 바와 같이 마르텐사이트로 변태시키기 위해서는 우선 오스테나이트 상태로 가열해야만 하는데, 그때의 가열조건, 특히 가열온도는 강의 성질에 중대한 영향을 미치므로 가열온도의 선정은 무엇보다도 중요하다. 여기서 우선 정확히 규정해야 할 것은 용어문제로서, 상황에 따라서 가열온도, 퀜칭온도 및 오스테나이트화 온도를 구분해서 사용하기도 하지만 본절에서는 이 3가지 용어를 동일한 의미로써 사용한다. 퀜칭을 위한 가열온도는 수냉하는 경우, 아공석강에서는 Ac3 변태점 이상 30∼50℃ 정도, 과공석강에서는 Ac1 변태점 이상 30∼50℃ 범위로 하는 것이 보통이며, 유냉의 경우는 이것보다 다소 높은 온도를 사용한다. 가열온도가 이 온도범위보다 높아짐에 따라서 오스테나이트의 결정립은 점차 크게 성장하여 조대화되기 쉬워진다. 그런데 과공석강에서는 오스테나이트화 온도에서 오스테나이트와 미용해 탄화물이 공존하는데, 이 탄화물이 오스테나이트 결정립계의 이동, 즉 결정립성장을 방해하는 효과가 있다. 미용해 탄화물이 조대하거나 그 수가 적으면 그만큼 결정립은 조대해진다. 한편 아공석강에서는 오스테나이트화시 모든 탄화물이 고용되므로 결정립성장은 매우 빠른 속도로 진행된다. 이와 같이 결정립이 조대해지면 마르텐사이트변태가 용이하여 열처리가 다소 쉽게 되기는 하지만 열처리후의 인성은 현저하게 감소된다. 표 4.2는 베어링강 2종(STB 2 : 1%C, 1.3%Cr)의 직경 8mm의 환봉을 유냉했을 때와 마르템퍼링(후술)했을 때 인성에 미치는 오스테나이트화 온도의 영향을 나타낸 것으로, 어떤 경우도 오스테나이트화 온도가 상승함에 따라 인성이 감소됨을 알 수 있다. 표 4.2 베어링강을 유냉 및 마르템퍼링 처리시 오스테나이트화 온도에 따른 인성변화

그러나 공구강의 경우는 오스테나이트화시에 탄화물을 적당히 고용시켜서 마르텐사이트를 충분히 단단하게 하는 동시에, 잔류오스테나이트량을 줄이는 것이 동시에 중요하다. 탄소공구강에서는 상기와 같은 온도범위를 선택하면 별다른 문제는 없지만, 과공석강의 경우 온도가 지나치게 높으면 오스테나이트중의 탄소량이 많아져서 MS점이 저하하고, 상온으로 냉각시 잔류오스테나이트가 많아져 충분한 경화가 안될 뿐 아니라 열균열도 일어나기 쉽게 된다. 한편 고속도공구강 등과 같이 W이나 Cr 등 탄화물을 만들기 쉬운 합금원소를 다량 함유한 강에서는 이들의 원소 때문에 공석변태점이 상승하는 동시에 오스테나이트중의 탄소고용도가 감소한다. 예를 들면 18%W-4%Cr-1%V형의 고속도강(SKH2)에서는 공석점이 850℃ 정도까지 상승되므로 900℃ 부근으로 가열해도 오스테나이트의 탄소농도는 0.20∼0.25% 정도이므로 경도가 겨우 HRC 50정도밖에 되지 않는다. 가열온도를 높이면 점점 탄화물의 고용량이 증가하여 1300℃ 부근에서는 약 0.55% 정도의 탄소가 고용해서 퀜칭경도는 HRC 66∼67로 충분히 높아진다. 또한 고용된 W, Cr과 같은 합금원소때문에 현저하게 열처리하기 쉽고, 또 고속절삭으로 날끝온도가 상승해도 쉽게 경도가 저하되지 않는 우수한 템퍼링연화저항성이 얻어지는 것이다. 그러나 이 경우도 지나치게 온도가 높아지면 역시 결정립의 조대화로 인해 취화된다. 이와 같이 강의 성질이 손상될 만큼의 고온까지 가열시키는 것을 과열(過熱, overheat)이라 한다. 더우기 그 정도가 더욱 심하여 입계가 일부 용융하기 시작한다든지 입계를 따라 내부까지 산화가 진행되어 나머지 열처리나 기계가공 등의 작업에서도 정상적인 성질을 회복할 수 없다든지 하는 경우를 버닝(burning)이라고 한다. ② 가열시간 또한 오스테나이트화시에는 가열시간도 중요하다. KS 규격에서도, 여러 회사의 카탈로그에서도 퀜칭온도(오스테나이트화 온도)는 규정되어 있지만 가열시간, 특히 오스테나이트화 온도에서 유지하는 시간에 대한 규정은 찾아볼 수 없다. 그러나 열처리란 가열온도, 가열시간 및 냉각의 조합이므로 필수적으로 가열시간이 필요하다. 작업능률이나 원가 등의 입장에서는 가열시간은 가능한한 짧을수록 바람직하지만, 실제로는 가열방법이나 재료의 크기에 따라 그 중심부까지 필요한 온도로 상승시키기 위한 시간과 확산에 의해 탄화물이 고용되어 균일한 오스테나이트로 형성되는데에 필요한 시간을 생각해야 한다. 합금원소가 많이 함유될수록 일반적으로 열전도율은 적고 또 확산속도도 늦으므로 장시간의 가열이 필요하다.

그림 4. 13. 가열시간의 정의 한편 오스테나이트화 처리시의 가열시간은 승온시간(昇溫時間), 균열시간(均熱時間) 및 유지시간(維持時間)으로 이루어져 있다. 승온시간이란 부품의 표면이 소정의 오스테나이트화 온도로 도달되는데 필요한 시간을 말하고, 균열시간이란 부품의 표면과 중심의 온도가 일치하기까지의 시간을 말하며, 유지시간이란 부품 전체가 그 온도에서 유지되는 시간을 말하는 것이다. 따라서 " 승온시간 + 균열시간 + 유지시간 = 가열시간" 이란 관계가 성립된다. 여기서 우리가 주의해야 할 사항은 그림 4.13에서도 알 수 있듯이 로내온도의 승온속도와 부품의 승온속도가 다르다는 것이다. 따라서 여기서 사용되는 「온도」라는 말은 부품의 실제온도를 의미하는 것으로, 로내분위기 온도 즉 온도계로 지시되는 온도가 아니다. 승온시간은 부품의 크기에 따라서 달라지지만 유지시간은 부품의 크기에는 별 영향이 없고, 강종에 따라서 달라진다. 즉
승온시간 = f (부품의 크기) 유지시간 = f (강종) ---- 아공석강인가 과공석강인가에 따라 다르다. 승온시간 + 유지시간 = 가열시간(soaking time)
여기서 가열시간에는 표면과 중심부의 승온시간의 차이, 즉 균열시간도 포함되어야 하지만 그 시간의 차이는 의외로 작다. 다시 말해서 표면이 퀜칭온도에 도달하면 중심부도 거의 동시에 그 온도에 도달된다고 보아도 좋다는 것이다. 그림 4.14는기계구조용강의 실측결과로서, 표면과 중심의 승온시간의 차이는 직경 100㎜의 환봉에서는 보통가열시 2분, 급속가열시 5분이다. 따라서 종전에 25㎜당 30분이라고 하는 것은 유지시간을 의미하는 것이 아니라 승온시간을 포함하는 말이다. 따라서 아공석강이나 공석강에서는 A3 변태온도 이상 50℃로 가열되는 동안에 거의 완전히 오스테나이트로 변태되므로 유지시간이 필요없으나, 과공석의 탄소공구강이나 합금공구강 또는 고속도강 등과 같은 고탄소 고합금강에서는 오스테나이트 중에 어느 정도의 탄화물을 고용시킬 필요가 있으므로 10∼30분 정도의 유지시간이 필요하다. 
그림 4. 14. 강재의 표면온도 도달 후 중심부에 도달하기까지의 시간

-
그림 4.15. 퀜칭, 템퍼링에 의한 미세구상 시멘타이트 조직과 구상화처리에 의한 조대구상 시멘타이트 조직의 - 오스테나이트화 곡선의 비교(1%C의 탄소강, 750℃오스테나이트화)
한편 탄화물이 오스테나이트에 고용되는 고용속도는 강종에 따라 틀려지는데, 특히 텅스텐이나 바나듐과 같은 강력한 탄화물 생성원소를 함유한 강은 현저하게 늦어지지만, 동일강종이라도 퀜칭전의 조직, 주로 탄화물의 크기나 분산상태에 따라서 큰 영향을 받는다. 그림 4.15는 1%C의 탄소강을 750℃에서 오스테나이트화한 경우로서, 구상화처리를 한 조대한 구상시멘타이트를 함유한 강이 그 고용속도가 늦으므로 오스테나이트화도 늦다는 것을 알 수 있다. 이와 같이 탄화물이 조대한 구상 혹은 망상을 나타낼 때는 고용속도가 늦으므로 퀜칭전에 탄화물이 미세하고 균일하게 분산된 상태가 되도록 구상화풀림이나 노멀라이징 등의 예비처리를 할 필요가 있다.

고탄소저크롬 베어링강에서 탄화물이 고용에 필요한 시간은 900℃의 경우, 미세펄라이트조직에서 약 2분, 펄라이트조직에서 약 3분, 구상화조직에서 1시간 이상이 필요하다고 한다. 그림 4.16은 구상화처리한 베어링강을 여러가지 온도로 오스테나이트화 했을 때의 유지시간과 미고용 탄화물량의 관계를 나타낸 것으로, 탄화물량이 일정값으로 안정화될 때까지 약 30∼50분간이 소요되고 있지만, 탄화물이 완전히 고용되면 퀜칭했을 때의 잔류오스테나이트도 많아지고, 경도도 저하되며, 결정립의 조대화, 열균열, 시효변형등의 여러가지 문제가 발생될 수 있으므로 실제로는 반드시 평형상태까지 탄화물을 고용시킬 필요는 없다. 그리고 전술한 중심부와 표면의 승온시간의 차이도 고려해서 각 강종의 오스테나이트화 온도로의 적당한 가열시간을 선정해야 하는데, 탄소강이나 특수공구강(STS)에서 살두께 25mm당 약 30분, 다이스강(STD)에서 그 1.5배 정도, 또 스테인리스강 등은 2배인 60분 전후를 유지한다. 고속도공구강은 1200∼1350℃에서 퀜칭하지만, 그로 인한 가열에는 염화바륨(BaCl2) 용융염욕을 사용하는 경우가 많고, 차가운 강재를 직접 고온염욕 중에 넣으면 균열이 생길 위험이 있으므로 1회 또는 2회의 예열을 해주는 것이 좋다. (3) 예열 퀜칭의 첫번째 단계는 예열(豫熱, preheating)로부터 시작된다. 즉 오스테나이트화의 전단계이다. 예열하는 목적은 부품의 전단면을 가능한한 균일하게 승온시켜서 열처리변형을 경감시키기 위한 것이다. 특히 염욕가열과 같이 급속가열되는 경우에는 예열이 필수적이다. 아공석강이나 저탄소강에서는 그렇게 예열이 필요하지는 않지만, 고탄소고합금공구강(STD 11)이나 고속도공구강 등에서는 열전도도가 작고, 탄화물이 많이 존재하기 때문에 예열이 필요하다. 예열은 보통 1단예열만으로 충분하지만, 형상이 복잡한 금형에서와 같이 특별히 신중을 기하고자 할 때에는 2단예열을 채용하는 것이 좋다. 1단예열은 변태점 직하, 즉 650∼700℃의 온도범위를 선택하는 것이 좋다. 왜냐하면 변태점에서 펄라이트가 오스테나이트로 변태할 때에 체적이 수축하므로 변태전에 부품 전단면을 균일한 온도로 하여 변형을 방지하기 위해서이다. 2단예열온도는 강이 탄성체에서 소성체로 변하는 온도, 즉 450∼500℃의 온도범위를 선택하는 것이 좋다. 이것은 강이 소성체일 때에 변형이 일어나기 쉽기 때문이다. 한편 예열을 위한 가열시간은 25㎜당 약 40분 정도가 좋다. 이정도의 시간이면 부품의 중심부까지 예열온도에 도달된다. 그리고 유지시간은 필요치 않다. (4) 냉각매체 강을 퀜칭할 때 복잡한 형상의 고합금강에서는 간혹 공랭이라고 하여 단순히 공기중 방랭(放冷)만으로 마르텐사이트조직을 얻을 수 있는 경우도 있지만, 그 외의 경우는 물 또는 기름 속에 투입해서 급랭하는 것이 보통이다. 잘 알려진 것처럼 기름보다 물에서의 냉각속도가 빠르지만 기름이나 물도 그 온도에 따라, 혹은 첨가물에 따라, 혹은 교반하는 정도에 따라서도 그 냉각능력은 변화된다. 일정한 조건으로 수냉한 경우에도 강재가 냉각되는 과정이 단순하지만은 않고 냉각도중에 냉각속도는 커지거나 작아지게 되어 미묘하게 변화한다. 그림 4.17은 직경 12.7㎜(0.5 in.)의 강봉을 수냉했을 때의 냉각곡선을 표시한 것으로 냉각상황은 대략 3단계로 구분된다.

그림 4.17. 수냉시의 냉각단계 ① 제 1 단계 : 가열된 강재의 표면에 증기막이 생겨서 열전도도가 작아지므로 강의 냉각은 비교적 늦다. 이 단계를 증기막단계라고 한다. ② 제 2 단계 : 강표면에서 심한 비등이 일어나고, 증기막은 곳곳에서 파괴되어 기포로 되어 없어지므로 강표면은 직접 물과 접촉해서 전도와 대류에 의해 열이 방출되어 급속히 냉각된다. 이 단계를 비등단계라고 한다. ③ 제 3 단계 : 수증기의 발생은 없고, 강의 온도와 물의 온도의 차가 적어지므로 다시 냉각속도는 늦어진다. 이 단계를 대류단계라고 한다.
강의 퀜칭시에는 펄라이트변태가 일어나기 쉬운 A1∼550℃간의 온도범위를 충분히 급랭시켜야 한다. 그렇게 하기 위해서는 특히 제 1단계가 나타나는 시간을 되도록 짧게 할 필요가 있는데, 그것은 수중에서 8자의 형태로 강재를 강하게 흔들어 준다거나 물을 심하게 교반시켜서 수증기막이 빠르게 파괴되도록 하면 된다. 또한 수온을 되도록 낮추거나 5∼10% 정도의 식염이나 염화칼슘을 물에 녹이면 제 1단계는 단축된다. 그러나 Ar' 변태가 일어나는 온도범위를 충분히 빠른 속도로 냉각시키면 그 후의 냉각까지 반드시 빨리할 필요는 없다. 오히려 300℃ 이하에서 냉각속도를 늦출 수만 있다면 부품내외의 온도차를 줄이고, 변태응력의 발생이 적어져 열균열이나 열변형의 위험도 없어질 것이다. 즉 약 550℃ 부근까지의 냉각속도는 크고, 300℃ 이하에서의 냉각속도는 반대로 작아지는 냉각매체가 이상적이라 할 수 있다. Grossmann 등은 액의 냉각능력을 나타내는 일반적 수치로 퀜칭액과 강의 계면의 열전달계수 α와 강의 열전도도 λ의 비(H=α/λ)는 퀜칭액의 냉각능(冷却能, severity of quench)이라는 값을 쓰고 있다. 정지한 물의 냉각능을 1.0으로 하면 공기, 기름, 물 및 식염수의 H 값은 대략 표 4.3에 나타낸 바와 같은 값으로 된다. 이 표에서 보면 물이나 기름을 심하게 교반할 경우 정지된 상태에 비해서 4배 정도까지 냉각능력이 크게 되므로 퀜칭할 때 교반이 대단히 중요한 의미를 가지고 있다는 것을 알 수 있다. 표 4.3 퀜칭액의 냉각능 H의 값 
(4) 냉각방법과 냉각효과 열처리에서 냉각속도의 중요성에 대해서는 재언을 요하지 않는다. 냉각속도에 따라서 강의 성질이 軟해지기도 하고 硬해지기도 한다. 냉각매체를 냉각제라고도 하는데, 여기에는 공기, 기름 및 물 등 여러가지가 사용되고 있다. 일반적으로 공기는 냉각속도가 느리고 기름, 물의 순서로 냉각속도가 빨라진다. 그러나 이러한 냉각매체에 따른 냉각효과는 절대적인 것은 아니고, 처리품의 크기에 따라서 변화된다. 즉 냉각제의 냉각속도는 냉각제 고유의 성질일 뿐이고, 그것에 따른 처리품의 냉각효과는 처리품의 크기에 따라서 달라지게 된다. 다시 말해서 냉각매체의 냉각속도와 처리품의 냉각효과는 항상 일치되지 않는다는 것이다. 표 4.3에서도 알 수 있듯이 냉각방법이 동일해도 냉각효과는 다르게 된다. 실제로 열처리에서 중요한 것은 냉각방법이라기보다는 냉각효과라고 할 수 있다. 노멀라이징은 대기중 방랭(放冷), 즉 공랭이라고 하는 냉각방법이 정의되어 있다. 그런데 소형부품을 방랭한 경우와 대형부품을 방랭한 경우에 냉각방법은 동일할지라도 처리품의 냉각효과는 달라진다. 따라서 대형부품에서는 방랭만으로는 냉각효과가 적으므로 선풍기 등으로 강제공랭(强制空冷)시켜야만 노멀라이징 효과가 얻어진다. 퀜칭시에도 마찬가지이다. 동일하게 유냉했다 할지라도 처리품의 크기에 따라서 냉각효과가 다르므로 퀜칭경화 정도도 달라진다. 소형품에서는 유냉을 해도 수냉과 동일한 효과가 있을 수 있고, 대형품에서는 공랭 정도의 효과만이 있어서 경화되지 않을 수도 있다. KS 철강핸드북에 노멀라이징은 공랭, 풀림은 노냉, 그리고 탄소공구강(STC)의 퀜칭은 수냉, 고속도강(SKH)의 퀜칭은 유냉, STD 11과 같은 합금공구강의 퀜칭은 공랭 등으로 규정되어 있지만, 이것은 일본공업규격(JIS)에 따르면 표준시험편의 크기(15㎜φ×20㎜l)에 대한 것이므로 처리품의 크기에 따라서 적당히 냉각방법을 달리 하지 않으면 안된다. (5) 형상에 따른 냉각효과
처리품의 형상 중에서 가장 빠르게 냉각되는 것은 구형(球形)이고, 가장 느리게 냉각되는 형상은 판상(板狀)이다. 한편 하나의 제품에서도 부위에 따라 냉각효과가 다르게 된다. 평면에서의 냉각속도를 1이라 하면 二面角에서는 3, 三面角에서는 7정도로 되어 냉각속도가 커지는 반면에 凹面角에서는 오히려 1/3정도로 되어 냉각이 느려진다. 따라서 형상이 복잡한 제품일 때는 위치에 따라 냉각속도의 차이가 현저하므로 이로 인한 열처리변형이나 균열을 발생시킬 수도 있다. (6) 경화능 강의 퀜칭경도는 그림 1.1에서 나타낸 바와 같이 그 강의 탄소함유량에 따라서 결정되며, 합금원소와는 거의 관계가 없다. 0.6%C까지는 탄소량에 따라서 퀜칭경도는 증가하지만 그이상 탄소량이 증가되어도 퀜칭경도는 그다지 증가되지 않는다. 또한 동일한 탄소량일지라도 마르텐사이트 조직은 미세펄라이트나 구상화조직에 비해서 훨씬 경도가 높다. 이것이 퀜칭열처리를 통해서 마르텐사이트로 변태시키는 우선적인 이유이다. 그러나 퀜칭열처리는 0.3%C 이상의 탄소를 함유한 강에서만 주로 행하여지고, 0.3%C 이하의 탄소를 함유한 강에서는 페라이트-펄라이트 조직으로 만들어 사용하는 것이 보통이다. 이것은 0.3%C 이하에서는 퀜칭경도가 그다지 높지 않기 때문이다. 한편 강에서 퀜칭되는 깊이는 C%가 많을수록, 합금원소량이 많을수록, 그리고 결정립이 조대할수록 커지게 되는데, 이중에서 가장 크게 영향을 미치는 인자는 합금원소이다. 그러므로 퀜칭시에 경도를 향상시키는데에는 탄소량 증가가 효과적이고, 경화깊이를 크게 하는데에는 합금원소 첨가가 효과적이라는 사실을 기억해야만 한다. 1) 경화능의 정의 동일한 크기의 제품일지라도 강종에 따라 퀜칭시 경화되는 깊이가 다르다. 이 경화깊이를 지배하는 강자체의 성능을 경화능(硬化能, hardenability)이라고 한다. 따라서 동일한 냉각매체로 퀜칭시 경화깊이가 큰 강은 경화능이 좋고, 반대로 경화깊이가 작은 강은 경화능이 나쁜 강이라고 불리어진다. 이러한 점으로 보아 경화깊이는 합금원소 첨가로서 커지므로 탄소강은 경화능이 나쁘고, 합금강은 경화능이 좋아지게 된다. 경화능을 알기 위해서는 퀜칭된 강의 단면경도분포를 측정하면 된다. 큰 강재를 퀜칭하면 표면만 경화되고 중심부는 냉각속도가 느리므로 Ar'변태를 일으켜서 경화되지 않는다. 따라서 단면경도분포는 U자형을 나타낸다. 이것을 U곡선이라고 한다.된다. 한편 동일한 강종일지라도 제품의 크기(질량)에 따라 경화깊이가 달라진다. 탄소강인 SAE 1045강과 합금강인 6140강에 대해서 고려해 보면 SAE 1045강에서 보면 환봉직경이 커짐에 따라 표면경도가 급격한 감소를 보이고 있고 중심부경도도 연속적인 감소를 나타내고 있다. 이와 같이 제품크기가 클수록 퀜칭경도가 감소하는 현상을 질량효과(質量效果, mass effect)라고 한다. 반면에 합금강인 6140강에서는 어떠한 환봉직경에서도 1045강보다 경도가 높다. 그럼에도 불구하고 강재표면으로부터 중심부까지의 경도의 편차는 여전히 존재하고 있으며 특히 직경이 클수록 이 차이는 심하다. 이상에서 알 수 있듯이 일반적으로 탄소강은 질량효과가 크고, 합금강은 질량효과가 크다. 따라서 합금강은 제품의 크기가 클지라도 경화시키기가 용이하다. 퀜칭할 때에는 강재의 경화능과 질량효과를 고려해서 냉각제의 선택 및 퀜칭방법의 검토가 필요하다. 2) 경화능의 표시방법 임계냉각속도가 큰 강은 단면치수가 약간 커져서 중심부의 냉각속도가 작아지면 경화되지 않는다. 즉 경화능이 나쁘다. 반대로 임계냉각속도가 작은 강은 어느 정도의 두께에서는 중심부까지도 경화될 수 있다. 즉 경화능이 좋다. 따라서 경화능이 좋고 나쁜 것은 임계냉각속도가 작고 큰 것과 직접적으로 관계되므로 임계냉각속도는 경화능의 표시방법으로서 이용된다. 그러나 임계냉각속도가 몇 ℃/초일 때 몇 mm의 깊이까지 완전히 경화되는지, 또 어느 정도의 크기일 때 어떤 냉각을 하면 표면으로부터 몇mm까지 경화되는지에 대한 실용적인 수치를 곧바로 얻기는 곤란하다. 오히려 『중심부까지 경화되는 임계직경』,또는 수냉면으로부터 어느 경도이상되는 깊이가 몇mm인지를 구하는 편이 경화능을 나타내는데 보다 실용적이다. 여기서 후자는 『一端퀜칭방법』에 의한 경화능시험으로서 KS규격에도 규정되어 있고, 또 전자의 『임계직경에 의한 방법』은 전술한 냉각제의 냉각능 H와 함께 잘 연구되어 화학조성으로부터 강의 경화능을 예상하는 방법까지 거의 확립되어 있다. ① 임계직경에 의한 경화능 표시방법 경화능은 보통 퀜칭경화층의 깊이로서 결정한다. 이 때 경화층의 깊이를 결정하기 위해서 일반적으로 50%마르텐사이트조직의 경도인 HRC 50(HV=513)을 임계경도(臨界硬度, critical hardness)라고 하며, 중심부의 경도가 임계경도인 HRC 50을 나타내는 강재직경을 임계직경(臨界直徑, critical diameter)이라고 한다. 또한 강재표면으로부터 50%마르텐사이트 부분까지의 깊이를 퀜칭경화층깊이, 그리고 중심부의 조직이 50%마르텐사이트로 되는 강재직경을 이상임계직경(理想臨界直徑, ideal diameter)라고 한다. 50%마르텐사이트를 임계직경의 기준으로 선정하는 이유는 퀜칭된 환봉의 단면을 나이탈(nital)로 부식시키면 50%마르텐사이트-50%펄라이트 지역에서 경화부와 비경화부 사이의 부식濃淡의 차이가 매우 현저하고, 또 50%마르텐사이트 지역이 임계경도인 HRC 50에 거의 해당하기 때문이다. Ni-Cr강인 KS SNC 236강(JIS SNC 1강, AISI 3140강)을 수냉 및 유냉하였을 때 강봉 직경에 따른 중심부경도의 변화를 살펴보면 강재 직경에 따른 중심부경도의 급격한 변화는 임계경도인 HRC 50과 거의 근사하다는 사실을 알 수 있고, 또 이 임계직경은 냉각제의 종류에 따라 다른데 유냉시에는 1.25", 수냉시에는 1.83"로 수냉시가 크다는 것을 알 수 있다. 이 임계직경은 강의 화학조성과 결정립도에 따라서 결정되는 강 고유의 성질이며 경화능의 비교기준으로서 이용되고 있다. ② 일단(一端)퀜칭방법에 의한 경화능 일단퀜칭방법에 의한 경화능시험(end-quench test)은 Jominy와 Boegehold에 의해 처음 시작되었다. 죠미니시험(Jominy test)이라고도 하며 기계구조용 탄소강 및 저합금강의 경화능시험에 많이 이용되고 있다. 시험편은 직경 25mm, 길이 100mm의 원주상으로 되어 있고, 一端에 직경 28mm의 플랜지를 달고 있다. 시험장치는 일정한 유량 및 유속으로 물을 분출시켜 시험편 밑의 단면에만 분출된 물이 충돌해 그 일단만이 냉각되도록 되어 있다. 분출되는 물의 강도를 일정하게 하기 위해서는 시험편을 올려놓지 않을 때의 자유높이를 65±10mm로 규정하여 이 자유높이가 일정하게 유지되도록 넘쳐 흐르는 장치를 이용하여 낙차를 일정하게 한 물탱크나 또는 물펌프를 사용한다. 시험편은 로중에서 정해진 온도로 가열을 한 후 꺼내어 5초 이내에 이 시험장치에서 분출되는 물에 의한 퀜칭이 되도록 한다. 시험편의 측면에서의 공기나 복사에 의한 냉각은 분수에 의한 하단부로부터의 냉각에 비해 무시할 수 있을 만큼 적으므로 시험편은 하단으로부터 위로 갈수록 점차 냉각속도가 작아진다. 즉 1개의 시험편에서 여러가지 냉각속도를 얻을 수가 있게 된다. 이렇게 해서 퀜칭이 끝난 시험편의 원주면을 축방향에 따라 깊이 약 0.4mm씩 연삭해서 평행한 2면을 만들고, 이 면을 퀜칭단으로부터 1.5mm씩 일정한 간격으로 경도를 측정하여, 퀜칭단으로부터의 거리에 따른 경도변화를 그래프에 나타낸다. 이 곡선을 경화능곡선(硬化能曲線, hardenability curve, H-curve), 또는 죠미니곡선이라 한다. 한편 경화능을 나타내는데에는 경화능곡선 이외에도 경화능지수를 사용할 수 있는데, 이것은 퀜칭단으로부터 일정거리에서의 경도 또는 일정경도에 대한 퀜칭단으로부터의 거리이다. 경도시험에서 특정경도를 지정하는 경우 보통은 마르텐사이트와 미세펄라이트가 50%씩인 위치의 경도를 택할 때가 많다. 그것은 조직이 100% 마르텐사이트 부분으로부터 미세펄라이트로 변화되는 도중 50% 마르텐사이트 부근이 가장 급격하게 조직이 변화되는 부분이며, 이에 따라 경도변화도 현저하므로 경도곡선이나 조직관찰로부터 50% 마르텐사이트가 존재하는 위치를 결정하는 것이 쉽고 오차도 적기 때문이다. 그러나 미세펄라이트가 혼합되어 있으면 기계적성질은 좋지 않으므로 큰 힘이 가해지는 부분은 적어도 90% 이상의 마르텐사이트조직이 되도록 퀜칭하는 것이 바람직하다. 더우기 일단퀜칭시험에서는 일정한 치수의 시험편을 일정한 방법으로 퀜칭하므로 그 특정부분의 냉각속도는 항상 같고, 그 값은 각 부분에 대하여 측정되어 있다. 따라서 여러가지 직경의 환봉에 대하여 물이나 기름에 퀜칭했을 때의 냉각속도를 측정해두면 일단퀜칭시험편의 각 부분의 냉각속도와 대응시킴으로 일단퀜칭시험의 결과로부터 환봉의 퀜칭경화층 깊이를 예측할 수 있다. |
◆ 심랭처리 ⑴ 목적 前章에서 나타낸 바와 같이 탄소량이 증가함에 따라 MS와 Mf점이 저하되는데, Mf점이 상온이하인 경우에는 퀜칭시 잔류오스테나이트(γR)가 존재하게 되며, 그 양은 고탄소강일수록 즉 MS점이 저하될수록 증가된다. 같은 이유로 과공석강에서는 오스테나이트화 온도가 높을수록 탄화물의 고용량이 증가되므로 잔류오스테나이트량이 증가된다. 한편 퀜칭시의 냉각속도도 잔류오스테나이트량에 영향을 미치는데, 동일한 강일지라도 유냉하는 편이 수냉하는 것보다 γR량이 많아진다. 이와 같이 잔류오스테나이트가 존재하면 퀜칭경도의 저하, 치수불안정 및 연마균열 등의 문제점이 따르므로 퀜칭한 강을 0℃ 이하의 온도로 냉각하여 γR을 마르텐사이트화 하는 처리를 심랭처리(深冷處理, subzero treatment)라고 한다. 이 처리에 의해서 잔류오스테나이트가 마르텐사이트로 변태하므로 퀜칭경도가 증가되고, 경도를 균일화시켜서 내마모성을 향상시키며, 또한 치수안정성을 제고시키는 등 매우 중요한 효과를 얻을 수 있다. 공구강(STC, STS, STD)이나 고속도강 및 침탄처리품 등에는 필요한 처리이다. (2) 방법 일반적으로 퀜칭후 곧바로 심랭처리하는 것이 보통이다. 제품두께가 크다거나 예리한 모서리가 존재할 경우에는 심랭처리시 균열을 발생시키기 쉬우므로, 심랭처리하기 전에 100℃의 물속에서 1시간 정도 템퍼링하여 균열발생을 방지하는 것이 좋다. 심랭처리시 처리온도에서의 유지시간이 꼭 필요하지는 않지만 일반적으로 25mm당 30min 유지하고 있다. 심랭처리온도로부터 상온으로 가열하는데에는 공기중에서 방치하는 自然解凍方法도 있지만 작업성이나 잔류응력해소라는 면에서는 水中에 투입하여 急速解凍(up-hill quenching)시키는 것이 좋다. 심랭처리에 사용되는 냉매로는 다음의 2가지가 있다. ① 드라이아이스 단열재가 내장된 스테인리스강제 통속에 드라이아이스와 알콜을 넣어서 -78℃로 유지하여 제품을 침적시킨다. 이 냉매로는 -100℃ 이하에서만 처리할 수 있기 때문에 보통심랭처리(普通深冷處理)라고 부른다. ② 액체질소 액체질소를 그대로 사용하는 액체법과 분사시켜서 사용하는 가스법이 있다. 이 냉매로는 -196℃에서 처리가 가능하므로 초심랭처리(超深冷處理)라고 부른다. 超深冷處理는 Cryo-treatment라고도 불리어지며, Cryo-tec, Cryotough, Ellenite, Perm-O-Bond 등의 상표명으로 공업화되어 있다. (3) 초심랭처리의 장점 1) 강 퀜칭한 강에는 잔류오스테나이트(γR)와 잔류응력(σR)이 존재한다. 일반적으로 γR은 약 300℃ 이상에서 템퍼링하면 소멸하고, σR은 약 450℃ 이상으로 가열하면 해소될 수가 있다. 따라서 구조용강은 600∼650℃에서 템퍼링하므로 심랭처리가 필요치 않지만, 내마모용으로 사용되는 침탄부품, 고주파경화부품, 베어링강 및 탄소공구강 등은 200℃ 정도의 저온템퍼링이 적용되므로 심랭처리가 필요하게 된다. 또한 STD 11강이나 고속도강과 같이 500∼600℃에서 2차 내지 3차템퍼링까지 하는 강종들도 심랭처리하면 1차템퍼링만으로 족하므로 심랭처리의 필요성이 크다. R.F.Barron의 연구결과17)에 의하면 초심랭처리에 의해서 다음과 같은 결과가 얻어진다. ① 잔류오스테나이트가 거의 전부 마르텐사이트로 변태된다. ② 보통열처리품이나 보통심랭처리품보다도 내마모성이 현저히 향상된다. ③ 조직의 미세화와 미세탄화물의 석출이 이루어진다. ④ 보통심랭처리품에 비해서 경도의 변화는 거의 없다. 일반적으로 초심랭처리에 의한 경도증가는 보통심랭처리에 비해서 거의 차이가 없으나, 내마모성은 초심랭처리한 경우가 보통심랭처리한 경우보다 약 2∼3배(非심랭처리품에 비해서는 2∼6.6배)정도로 현저하게 향상된다. 현재 내마모성의 평가가 주로 경도비교로써 이루어지고 있는 현실을 감안할 때 위의 사실은 이러한 내마모성에 대한 고정관념에 위배되는 것이다. 따라서 경도비교만으로 내마모성을 평가해서는 안된다는 사실에 유의해야만 한다. 일본 日立製作所 勝田工場의 연구결과를 보면 STD 11강으로 만든 강판 냉간압연용 롤은 초심랭처리에 의해서 내마모성이 2∼3배 향상되었다고 보고하고 있다. 한편 초심랭처리는 오스테나이트계 스테인리스강에도 효과적인 것으로 알려지고 있다. Al-Tech Speciality Steel Corp., N.Y.의 보고에 따르면 STS 302의 스프링에 초심랭처리를 행하면 인장강도 200 kg/mm2, 비틀림 항복점 100kg/mm2(초심랭처리후 425℃×30분 응력제거처리)로 되어 미처리품보다도 30% 강도증가효과가 있고, 중량은 60%정도 가벼워진다. 또한 초심랭처리는 비철합금에도 매우 효과적인데, 스포트 용접기용 Cu전극(5%Cr동)에 초심랭처리를 행하면 전극단면의 마모나 소성변형이 작아져서 수명이 3∼5배 증가되고, Al합금에서도 시효촉진과 기계적성질의 개선효과가 있으며, 초경합금이나 기타 소결부품에서도 내마모성의 현저한 향상이 얻어진다.
|
◆ 템퍼링 (1) 목적 강재는 퀜칭상태 그대로 사용하는 일은 거의 없고, 보통 반드시 템퍼링을 한다. 그 이유로서는 다음과 같은 것을 들 수 있다.
- ① 퀜칭시에 형성되는 내부응력(內部應力, internal stress) 때문에, 연삭 등의 다듬질 가공을 하면 응력의 균형이 달라져 변형이나 균열을 발생시킬 수 있고, 또 그대로 사용하면 시간이 경과함에 따라 응력이 완화되는 동시에 변형이 나타나게 된다.
② 마르텐사이트조직은 일반적으로 매우 단단하기 때문에 취약한 성질을 갖고 있다. 또한 높은 경도에 비해 인장강도가 반드시 높다고 할 수는 없으며, 항복점이나 탄성한계도 낮다. 이들의 경향은 탄소량이 많은 강일수록 심하다. 따라서 용도에 따라 적당한 인성을 유지하기 위해서 템퍼링을 해야만 한다. 특히 기계부품으로서 사용하기 위해서는 충분한 인성이 필요하기 때문에 500∼650℃ 정도의 고온에서 템퍼링을 한다. 이것은 템퍼링 마르텐사이트조직이 강도와 인성의 겸비라는 점에서 미세펄라이트보다 우수하기 때문이다. ③ 마르텐사이트는 조직은 불안정하여 과포화로 고용해 있는 탄소가 탄화물로서 석출하려는 경향이 강하고 여기에 수반해서 체적의 수축이 일어난다. 또 잔류오스테나이트가 함유되어 있는 경우에는 이것이 사용중에 마르텐사이트로 변태하여 체적의 팽창을 일으킨다. 이와 같이 마르텐사이트도 잔류오스테나이트와 같이 상온에서는 불안정하여 시간에 따라 상변화를 일으켜 부품의 형상이나 치수에 오차를 일으키므로 정밀한 공구나 기계부품 등에서는 주의해야만 한다. 150∼200℃에서의 템퍼링으로 경도를 크게 저하시키지 않고도 이와 같은 조직의 불안정성을 다소 제거할 수 있다. 이상과 같은 이유로부터 템퍼링을 한마디로 정의하면 퀜칭에 의해 형성된 불안정한 조직을 안정한 조직으로 변태시킴과 동시에 잔류응력을 감소시키고, 특히 인성을 개선시키기 위하여 A1점 이하의 적당한 온도로 가열유지 및 냉각하는 조작이라고 말할 수 있다.
(2) 방법
- ① 저온템퍼링
공구강 등과 같이 높은 경도와 내마모성을 필요로 하는 경우에는 주로 150∼200℃의 저온템퍼링을 해서 마르텐사이트 특유의 경도를 떨어뜨리지 않고 치수안정성과 다소의 인성을 개선시키고 있다. 템퍼링시간은 25mm 두께당 30분 유지하는 것이 일반화되어 있고, 템퍼링온도로부터의 냉각은 공랭을 한다. ② 고온템퍼링 기계구조용강 등과 같이 높은 인성을 필요로 하는 경우에는 400∼650℃의 온도범위에서 고온템퍼링을 실시하고 있다. 이와 같이 퀜칭.템퍼링에 의해서 인성을 향상시키는 열처리를 조질(調質)이라고도 부르고 있다. 템퍼링온도로부터의 냉각은 급랭(수냉이나 유냉)을 해야만 한다. 서냉을 하는 경우에는 후술하는 템퍼링취성(temper embrittlement)이 나타나기 때문이다.
(3) 템퍼링에 의한 조직과 성질의 변화 퀜칭상태의 마르텐사이트조직은 매우 불안정하고, 필라이트나 페라이트에 비해 현저하게 硬하다는 것은 이미 여러번 기술한 바 있다. 따라서 템퍼링의 목적은 전술한 바와 같이 퀜칭상태의 불안정한 마르텐사이트조직을 안정한 조직인 페라이트와 시멘타이트로 변화시키는 동시에 인성을 향상시키기 위한 것이다. 각 온도에서 탄화물이 석출되면 처음에는 경도가 약간 저하되지만 궁극적으로 커다란 감소를 가져온다. 잔류오스테나이트의 변태로써 어느 정도 경도에 기여하지만 이것은 기껏해야 탄화물석출에 의한 경도감소를 약간 지연시키는 효과밖에 없다. 따라서 템퍼링온도가 상승함에 따라 경도는 급격히 감소하게 된다. (4) 템퍼링취성 템퍼링온도가 높아짐에 따라 보통 경도와 인장강도는 감소하고, 연신율과 단면수축율 등은 증가되는 것이 일반적인 경향이다. 그러나 이와 함께 인성도 증가한다고 단언할 수는 없다. 실제로 어떤 특정한 온도범위에서 템퍼링하면 그 이하의 온도에서 템퍼링할 때보다 현저하게 취화되므로써 취성파괴(脆性破壞, brittle fracture)를 일으키는 일이 있다. 또 템퍼링온도로부터 서냉할 때에도 이와 같은 현상이 일어날 수도 있다. 이와 같이 퀜칭한 강을 어떤 온도에서 템퍼링을 했을 때 그 이하의 온도에서 템퍼링했을 때보다 오히려 취약하게 되는 현상을 템퍼링취성(temper brittleness)이라 한다. 따라서 실용강의 열처리시에는 이 점에 충분히 주의할 필요가 있고, 취화가 일어나지 않도록 적당한 템퍼링조건을 선택하여야 하며, 또 이것을 피할 수 없는 경우에는 그 위험성이 적은 다른 강종으로 변경하는 것이 바람직하다. 템퍼링취성은 300℃ 전후의 온도로 템퍼링한 경우에 나타나는 것과 보다 고온의 500℃ 혹은 그 이상의 온도로 템퍼링했을 때 나타나는 것의 2종류가 있는데, 전자는 저온템퍼링취성, 후자는 고온템퍼링취성이라 이름하고 있다. ① 저온템퍼링취성 일반적인 탄소강에 대하여 템퍼링온도에 따른 경도와 충격값의 변화를 살펴보면 경도는 템퍼링온도의 상승과 같이 단순하게 저하되어 가지만 충격값은 200℃까지의 템퍼링시에 일단은 증가하다가 200∼400℃에서는 오히려 현저하게 감소되고 있다. 이 온도범위에서는 경도나 인장시험결과에 이 취화와 대응하는 특별한 변화가 나타나지 않는다. 이 현상은 인(P)이나 질소(N)를 많이 함유한 강에 확실히 나타나고, 반대로 알루미늄(Al), 티탄(Ti), 붕소(B) 등을 첨가하면 취화가 적어진다. 이 취성이 나타나는 온도범위가 마치 템퍼링 제 2 단계의 온도범위와 일치하기 때문에 잔류오스테나이트의 분해가 취화원인이라고 생각되는 경우도 있다. 따라서 이 현상을 A취성이라 할 때도 있다. 그러나 0.15%C의 저탄소강에서 오히려 충격값의 저하가 현저하게 나타난다는 것, 또 심랭처리로 잔류오스테나이트량을 감소시켜도 동일하게 취화를 나타낸다는 점으로 미루어 보아 오늘날에는 잔류오스테나이트의 분해에 의하여 취화가 일어난다는 설은 옳지 않다고 여겨지고 있다. 그리고 현재도 역시 취성의 원인은 확실치 않지만 마르텐사이트의 템퍼링에 따라서 석출되는 매우 미세한 박판상 시멘타이트가 중요한 관계를 가지고 있다고 생각된다. 시멘타이트는 템퍼링 초기의 ε상으로부터 변해서 250℃ 부근에서 나타나기 시작하고 이것이 충분히 성장하면 인성은 증가하지만, 극히 미세한 간격을 가지는 어떤 특정한 크기가 되었을 때 강 전체를 취약하게 한다고 볼 수 있다. 그 원인이야 어쨋든간에 이러한 취화현상을 피하기 위해서는 200∼400℃의 온도범위에서는 템퍼링을 하지 않는 것이 보통이며, 많은 공구강이나 베어링강 등의 템퍼링온도를 150∼180℃로 선정하는 것도 이러한 이유 때문이다. 단 Si를 강에 첨가하면 이 취성이 나타나는 온도가 상승하여 300℃ 정도의 템퍼링에서도 특히 취화가 나타나지 않으므로 스프링강나 초강인강 등에서는 규소를 함유한 강을 이 부근의 온도에서 템퍼링하여 강도와 탄성을 향상시키고 있다.
② 고온템퍼링취성
고온템퍼링취성이라는 말은 보통 375∼575℃의 온도범위에서 템퍼링하거나 이 온도범위를 서냉한 시험편을 노치충격시험할 때에 노치인성의 감소, 즉 연성-취성 천이온도가 증가되는 현상을 말한다. Ni-Cr강을 400℃ 이상에서 템퍼링한 후 수냉시킨 경우와 서냉(노냉)시킨 경우의 충격값을 템퍼링온도에 대하여 살펴보면 450℃ 부근까지는 수냉 및 서냉시료 모두 급속히 인성이 증가하지만, 500∼550℃의 온도범위에서는 현저한 취화를 나타낸다. 또한 550℃ 이상에서는 수냉된 시료의 인성은 급속히 증가되지만 서냉시료는 수냉시료에 비해 대단히 취약하다는 것을 알 수 있다. 이 현상을 고온템퍼링취성이라 하는 것으로, 보통 간단히 템퍼링취성이라 하면 이 현상을 말하는 것이다. 또 500∼550℃에서의 템퍼링으로 생기는 취성을 1차 템퍼링취성, 다시 높은 온도의 텀퍼링후 서냉시에 나타내는 취성을 2차 템퍼링취성이라 구별할 때가 있다. 그러나 이 양자는 본질적으로 완전히 같은 현상으로 생각해도 된다. 요컨대 500∼550℃의 온도범위는 취화를 일으키는 온도범위이기 때문에, 이 범위에서 템퍼링하든지 혹은 이 범위를 통해서 서냉하는 경우에는 현저하게 취화를 일으킨다고 해석해야 한다. 이러한 취화는 0.6% 이상의 Mn(특히 1.5% 이상의 경우)을 함유한 망간강, 혹은 Cr 또는 Ni을 함유한 구조용 특수강에서 많이 나타나는 현상으로서, 저온템퍼링취성과 같이 인장시험결과나 그밖에 여러가지 물리적성질 등에는 거의 여기에 대응하는 변화는 확인되지 않고 오로지 충격시험의 경우에만 나타난다. 그러므로 충격적인 하중을 받는 기계부품에서는 이 취성에 특별히 주의해야 한다. 또한 이 취화현상은 단순히 상온에서의 충격값의 감소를 야기시킬 뿐만 아니라 사실은 충격천이온도를 상승시키기 때문에 더욱 문제시 되는 것이다. Cr강(SCr 440)을 620℃에서 2시간 템퍼링한 다음 급랭한 경우와 노냉한 경우로 천이온도곡선을 살펴보면 템퍼링온도로부터의 냉각속도가 느린 노냉시편의 천이온도는 70∼80℃ 상승하는 것을 알 수 있다. 이 고온템퍼링취성의 원인은 현재로서는 아직 확실하게 밝혀지지는 않았다. 그러나 조직시험이나 성분분석 등의 결과로부터 이 현상은 어떤 특정한 원소가 舊오스테나이트 결정립계(prior austenite grain boundary)에 편석됨으로써 일어난다는 것을 알 수 있었는데, 이들 원소중 가장 현저한 영향을 미치는 것은 Sb, Sn, P, As 등이다. 이러한 원소들은 매우 소량만 함유되어 있어도 템퍼링취성을 야기시킬 수 있게 된다. 특히 공업용강의 P함유량을 아무리 감소시켜도 템퍼링취성을 일으키기에 충분한 양이 된다. 전에는 이러한 예민화원소들의 舊오스테나이트 결정립계 편석을 확인하지 못했으나 근래에 템퍼링취성을 일으킨 강의 파면에 대하여 Auger분석을 행하므로써 구체적으로 확인되었다. 실제로 템퍼링취성을 일으키는 조건으로 열처리된 강의 舊오스테나이트 결정립계에는 결정립내보다 200배 정도로 P의 농도가 크다는 것이 밝혀졌다. 더구나 이 고농도의 P가 약 10Å 두께내에만 존재한다는 것이다. 그러나 여러가지 분석방법을 사용해 보아도 결정립계에는 어떠한 취약한 상도 형성되어 있지 않다는 사실을 확인하였다. Ni-Cr강(SNC 236)을 860℃에서 오스테나이트화 처리후 유냉하고, 625℃에서 1시간 템퍼링처리후 서냉 및 수냉한 시편을 관찰해 보면 서냉한 조직에는 舊오스테나이트 결정립계를 따라 성분원소의 편석이 보여지지만 수냉한 조직에서는 그러한 흔적을 볼 수 없다. 이러한 원인들을 분석해 봄으로써 고온템퍼링취성에 대한 방지책을 수립할 수 있다. 600℃ 이상의 온도에서 템퍼링하는 것, 그리고 템퍼링처리후 그 온도로부터 급냉시키는 것이 바람직하다. 강도 문제 때문에 600℃이하의 템퍼링이 요구되는 경우도 있지만 이 경우에도 템퍼링에 의한 취화를 피하기 위해 좀더 높은 온도를 사용하도록 하고 그대신 템퍼링시간을 단축시키면 되는 것이다. 단 치수나 두께가 큰 강재부품은 템퍼링후 급랭해도 중심부의 냉각속도가 느리기 때문에 취화를 피할 수 없는 경우도 있다. 그러나 이 때에는 Mo을 첨가하면 템퍼링취성을 방지할 수가 있다. |
◆ 강종에 따른 퀜칭 및 템퍼링방법 (1) 기계구조용 탄소강 탄소강은 질량효과가 크기 때문에 SM 50C에서도 경화되는 유효최대직경은 40mm 정도이므로 대형기계부품용으로는 적당치 않다. 오스테나이트화 온도는 풀림온도보다 약간 높게 하고, 냉각은 수냉으로 한다. 탄소강에서는 증기막 단계의 下限온도가 펄라이트변태 온도범위와 중첩되므로 靜水에서는 불완전 퀜칭되기 쉽다. 따라서 강하게 교반하여 증기막을 파괴시킬 필요가 있고, 水溫도 25℃ 이하로 유지하는 것이 좋다. 퀜칭경화깊이는 C나 Mn의 영향이 가장 크지만 Ni, Cr 및 B 등도 영향을 미치므로 scrap으로부터 혼입된 이들 불순물의 영향도 간과해서는 안된다. 템퍼링온도범위는 550∼600℃ 정도를 선택하여 소르바이트조직으로 만드는 調質처리가 행하여지고 있다. 침탄용강은 내마모성을 위하여 150∼200℃의 저온템퍼링을 행한다. (2) 기계구조용 합금강 기계구조용합금강의 탄화물은 M3C형의 複合탄화물이므로 오스테나이트에 고용하기 쉽다. 여기서 M은 금속원소를 나타내는 것으로, Fe의 일부가 다른 금속원소와 치환된 형태이다. 한예로 (Fe.Cr.Mo)3C와 같은 것이 있다. 기계구조용합금강의 퀜칭은 SMn계나 SCr계의 일부를 제외하고는 유냉이 원칙이다. 따라서 충분히 교반할 필요가 있고, 油溫도 60∼80℃ 정도로 유지하는 것이 좋다. 기계구조용 합금강의 템퍼링은 원칙적으로 550∼650℃의 고온템퍼링, 즉 조질처리가 행하여지고 있다. 그러나 SCr계와 같이 템퍼링연화저항성이 작은 강종은 약간 낮은 온도에서 템퍼링한다. 침탄용강은 역시 150∼200℃의 저온템퍼링을 행한다. 한편 전술한 바와 같이 일반적으로 저온템퍼링과 고온템퍼링의 중간온도에서는 템퍼링취성이 나타나서 충격인성이 현저하게 떨어지므로 이 온도범위에서의 템퍼링은 피하는 것이 좋다. 또 고온템퍼링후 서냉할 때에도 템퍼링취성이 나타나므로 KS규격에서도 템퍼링후에는 급랭하도록 규정하고 있다. 따라서 대형부품에서는 강제적인 냉각이 필요하게 되지만 일반적인 경우는 공랭정도면 충분히 템퍼링취성을 피할 수 있다. 물론 템퍼링취성의 방지 측면에서 볼 때에는 수냉이 가장 바람직하지만 수냉하면 변형과 녹 문제가 수반되므로 가능하면 피하는 것이 좋다. (3) 탄소공구강 고탄소강은 경화능이 나쁘므로 수냉으로 경화시킨다. 오스테나이트화 온도는 760∼820℃의 범위로, 온도는 정확히 조절하여 미용해 탄화물이 과잉으로 용해되지 않도록 한다. 온도가 너무 높으면 잔류오스테나이트량이 증가되어 퀜칭경도는 저하되고, 또한 퀜칭균열이나 변형이 발생되기 쉽다. 한편 고탄소강은 극히 탈탄되기 쉬우므로 가열시에 충분히 주의해야 하고, 필요에 따라서는 분위기 가열도 행한다. 탄소공구강은 STC 1∼STC 7까지 7종이 KS규격에 규정되어 있는데, 템퍼링은 모두 170℃ 전후에서 하도록 규정되어 있다. 일반적으로 템퍼링 오일에 의한 oil bath가 사용되고 있다. 이 강종은 템퍼링연화저항성이 없으므로 온도관리에 세심한 주의를 요한다. 템퍼링경도는 탄소량에 따라 HRC 54∼65 정도로 된다. (4) 합금공구강 합금공구강은 대부분 열전도도가 작으므로 800℃ 전후에서 예열을 행한다. 예열에 의해서 가열시의 변형을 방지하고, 오스테나이트화 온도에서의 유지시간을 단축시킬 수 있으며, 퀜칭경도의 균일화 등에 효과적이다. 오스테나이트화 온도는 강종에 따라서 매우 큰 차이를 보인다. 유지시간은 두께 25mm당 보통 15∼30분 정도로 한다. 냉각방법도 일정치 않고 강종에 따라 수냉, 유냉 및 공랭으로 규정되어 있다. 한편 템퍼링도 경도와 내마모성을 주로 요구하는 절삭용이나 냉간금형용 공구강은 저온템퍼링을 행하고, 충격인성이 요구된다거나 또는 열간금형용 공구강과 같이 고온에서 사용하는 강에서는 고온템퍼링을 행한다. 내충격용 공구강은 저온템퍼링하고 있지만 이 경우는 탄소량을 낮추거나 V을 첨가해서 인성을 확보하고 있다. STD 11과 같은 냉간금형용 합금공구강의 템퍼링온도가 150∼200℃로 규정되어 있는데, 실제로 금형을 열처리할 때에는 500℃ 부근에서 1차 템퍼링하고, 150∼200℃ 범위에서 2차 템퍼링하는 것이 좋다.
(5) 고속도강 고속도공구강은 합금원소량이 많으므로 2段 豫熱을 충분히 행하여야 한다. 오스테나이트화 온도에서의 유지시간은 3∼5분 정도면 된다. 오스테나이트화 온도는 탄화물을 충분히 고용시킬 필요가 있기 때문에 W계에서는 1300℃ 이상으로 매우 높지만, Mo계에서는 1250℃이하로서 충분하다. 그러나 두 경우 모두 통상적인 퀜칭에 비해서는 고온이므로 오스테나이트화 온도조절과 탈탄에 특별한 주의를 기울여야 한다. 일반적으로 가열은 염욕가열이 사용되고 있다. 한편 경화능이 좋으므로 공랭으로도 경화되지만 산화피막의 형성을 억제하기 위해서는 유냉으로 300℃ 정도까지 냉각시킨 후 꺼내서 공랭하는 것이 좋다. 고속도강에서 템퍼링온도에 따른 경도변화는 200∼400℃에서는 퀜칭에 의한 내부응력의 제거와 마르텐사이트의 분해 등에 기인하여 경도는 약간 저하되지만, 560∼600℃에서 템퍼링하면 재차 경도가 높아진다. 이것이 전술한 2차경화현상이다. 고속도강에서 나타나는 2차경화현상은
(ⅰ) 마르텐사이트로부터의 탄화물 석출 (ⅱ) 잔류오스테나이트로부터의 탄화물 석출 (ⅲ) 템퍼링온도로부터 냉각도중 일어나는 잔류오스테나이트의 마르텐사이트화 등 3가지 현상이 합성된 경화이다.
고속도강에서도 절삭내구력을 향상시키기 위해서는 2∼3회의 템퍼링이 필요하다. 즉 고합금공구강이나 고속도강에서의 잔류오스테나이트는 500℃부근의 템퍼링온도에서 냉각할 때 마르텐사이트로 변태한다. 따라서 이러한 강은 새롭게 생성된 2차 마르텐사이트에 인성을 주는 재템퍼링을 실시해야 된다. 만약 필요한 경도가 1차 템퍼링후 이미 도달되었다면 2차 템퍼링은 강의 경도가 감소되지 않도록 보다 낮은 온도에서 실시해야 한다. 실제로 이러한 2차 템퍼링은 1차 템퍼링보다 10∼30℃정도 낮은 온도에서 실시한다. 이렇게 함으로써 금형과 절삭공구의 인성과 내구성이 매우 향상된다. (6) 스프링강 및 베어링강 스프링강은 기계구조용강에, 베어링강은 합금공구강에 준해서 열처리하는 것이 보통이다. 스프링강은 탈탄, 표면흠 등에 의해서 피로한계를 뚜렷하게 저하시키므로 탈탄에 주의해야 하고, 특히 가열온도가 높으면 오스테나이트 결정립이 조대화되어 인성을 해치고, 표면상태가 나빠지며, 탈탄되기 쉬워지므로 조심해야 한다. 퀜칭시 300℃ 정도로 냉각되면 냉각유에서 꺼내어 연속적으로 템퍼링로에 장입한다. 템퍼링온도는 450∼540℃의 범위를 선택함으로써 탄성한계를 향상시키고 있다. 베어링강의 템퍼링온도는 강종과 형상에 따라 120∼200℃범위로 한다. 또 정밀한 것을 요구할 때에는 심랭처리와 템퍼링을 조합하여 數回 반복한다. |
◆ 특수 열처리 (1) 가공열처리 가공열처리(加工熱處理, thermo-mechanical treatment)란 소성가공(plastic working)과 열처리를 결합시킨 처리방법으로서, 이 방법은 보통의 열처리나 또는 소성가공을 독립적으로 사용했을 때 얻어질 수 없는 조직과 기계적성질을 얻고자 할 때 사용된다. 통상의 열간가공은 비교적 고온의 오스테나이트 영역에서 행하여지지만 최근 강의 강도와 인성을 향상시키기 위해 저온의 오스테나이트 영역에서, 또는 변태중이나 변태완료후에 가공을 행하므로써 바람직한 미세조직을 얻는 여러가지 처리법이 개발되어 주목을 끌고 있다. 이와 같은 가공열처리 방법은 고장력구조용강의 강도와 인성을 향상시키는 매우 중요한 방법으로서, 그중에서도 고장력저합금강(高張力低合金鋼, high strength low alloy steel : HSLA)의 제어압연(制御壓延, controlled rolling)은 널리 실용화되고 있다.
1) 안정한 오스테나이트 영역에서의 가공열처리 이 방법은 통상적인 열간가공에 가깝지만, 열간단조나 열간압연후 즉시 퀜칭을 행하므로써 경화능을 향상시켜서 강도와 인성의 개선을 꾀하는 처리이다. 제어압연에서도 안정한 오스테나이트 영역에서 가공을 행하지만 이것에 대해서는 후술하기로 한다.
2) 오스포밍에 의한 강화 대표적인 가공열처리 방법의 하나로서, 과냉(준안정)오스테나이트를 500℃ 부근에서 가공한 후 급랭함으로써 연성과 인성을 그다지 해치지 않고 강도를 대폭적으로 향상시킬 수 있다. 오스포밍에 의한 강화는 준안정 오스테나이트의 가공에 의한 마르텐사이트와 셀구조(cell structure)의 미세화에 기인하므로 탄소량이 적은 강에서는 강화를 기대할 수 없다. 3) 마르에이징강의 가공열처리 C를 함유하지 않은 마르에이징형 강력강에서는 오스테나이트의 가공에 의한 미세화로 강도의 상승을 기대할 수 없지만 연성과 인성이 향상된다. 특히 Co, Mo 및 Ti 등을 다량 함유한 인장강도 280kg/mm2 이상의 초강력 마르에이징강에서는 가공열처리에 의한 오스테나이트 결정립의 미세화가 파괴인성을 개선하는데에 매우 효과적이다.
4) 마르텐사이트 변태중의 가공 오스테나이트계 스테인리스강이나 고Mn강에서는 Ms점 이상의 온도에서 가공할 때에도 마르텐사이트를 형성시키지 않고 변형되어 현저하게 강화된다.
5) 페라이트 펄라이트 변태중의 가공 경화능이 그다지 크지 않은 저합금강을 변태점 영역에서 가공하는 조작을 아이소포밍(isoforming)이라고 부르는데, 이때 미세한 페라이트 결정립과 구상탄화물의 분산석출된 조직이 얻어지므로 강도와 인성이 향상된다. 근래의 제어압연강도 이 강화법을 이용하고 있다.
6) 펄라이트의 가공에 의한 강화 공석강에 가까운 0.7∼0.9%C강을 70∼90%로 냉간가공하면 300kg/mm2 이상의 높은 인장강도가 얻어진다. 이것이 피아노선으로서, 높은 강도와 우수한 피로특성을 이용하여 와이어 로프, 스프링, 프리스트레스트 콘크리트용 강선 등에 사용되고 있다. 이것은 심한 냉간가공을 행하여야 하므로 전처리로서 오스테나이트화처리후 500℃정도에서 항온변태시키는 파텐팅(patenting)처리가 필요하다. 이 열욕담금질법에 의해 미세균일한 펄라이트(소르바이트)조직이 얻어져서 연성이 커지므로 냉간가공성이 향상된다. 피아노선을 스프링으로서 사용하기 위해서는 냉간가공후 블루잉(bluing)이라고 부르는 350℃정도의 저온가열을 행한다. 이 처리로서 국부적인 변형의 제거, 시효경화현상에 의한 탄성한계의 상승, 또한 피로특성이 현저하게 개선된다.
7) 제어압연-제어냉각에 의한 강화. Nb, V 및 Ti 등을 미량첨가한 저탄소의 비조질 고장력강에서 열간압연과 냉각과정을 정밀하게 제어하면 압연상태에서 높은 강도와 인성을 얻을 수 있게 된다. 이 방법을 사용하면 공정단축에 의한 원가절감효과가 있으므로 크게 주목을 받고 있다. 제어압연-제어냉각에 의한 강인화기구는 다음과 같다.
- ① 압연전 slab의 가열온도를 가능한한 낮추어 압연전의 오스테나이트 결정립을 미세화시킨다.
② 오스테나이트 영역중 저온영역에서 충분한 가공을 행하여 재결정 오스테나이트 결정립의 미세화를 꾀한다. Nb, Ti 등의 합금원소를 미량 첨가하면 오스테나이트 결정립의 재결정성장을 억제해서 결정립미세화를 용이하게 한다. ③ 특히 Ar3 변태점 직상의 未재결정영역에서 가공을 행하면 오스테나이트 결정립은 길게 연신되고 동시에 결정립내에 변형대(變形帶)를 형성한다. 연신된 결정립계 및 결정립내의 변형대 경계는 페라이트 핵생성장소로 제공되므로 극히 미세한 페라이트 결정립이 얻어진다. ④ Ar3 변태점 이하의 2상영역까지 가공을 계속하면 미변태 오스테나이트 결정립은 보다 더 연신되고, 도입된 변형대의 밀도도 높아진다. 한편 변태가 완료된 페라이트 결정립내에는 가공에 의해 전위밀도가 높은 아결정립(亞結晶粒, sub-grain)이 형성되어 미립화가 더욱 진행된다. ⑤ 제어압연 종료후 적당한 속도로 가속냉각(수냉)하거나 급랭하는 도중에 공랭하는 등의 제어냉각을 행하므로써 강도의 대폭적인 향상이 이루어진다. 이것은 페라이트 결정립 자체의 강화, 미세화 및 펄라이트(베이나이트)분율의 증가에 기인하는 것이다.
인장강도 50kg/mm2급의 고장력강의 경우, 기본성분은 0.07∼0.15%C, 0.8∼1.5%Mn으로서 철강회사에 따라 큰 차이는 없지만 Nb, V, Ti, REM(희토류원소)의 미량첨가, Cu, Ni, Cr, Mo 등의 소량첨가 및 전술한 ①항에서 ⑤항까지의 각 공정의 온도, 가공도, 냉각속도 등의 선택은 회사에 따라 다르다. 이러한 강재를 TMCP(thermo-mechanical control process)강이라고 부르고 있는데, 이 TMCP강의 최종압연온도와 강도, 인성의 관계를 보면 가공온도의 저하에 따라 강도는 향상되지만, 인성치에는 최대치가 존재하여 Ar3점 이하 40℃의 온도영역(2상공존영역)에서 가공할 때가 가장 우수한 인성을 나타낸다. 또 Nb강은 Nb를 함유하지 않은 Si-Mn강에 비해 저탄소임에도 불구하고 높은 강도가 얻어지며, 특히 Ar3점 직하에서 가공시에 현저한 강도증가가 일어난다. 단 Ar3점 이하의 가공에서는 판두께 방향으로 항복점 이상의 큰 힘이 작용하는 경우 가공온도의 저하, 가공도의 증가와 함께 판두께 방향으로 박리되는 "separation" 이라 불리우는 결함이 발생하기 쉬우므로 이런 경우에는 가공온도를 낮게 할 수 없다. (2) 오스템퍼링 오스테나이트 상태로부터 Ms 이상의 어느 온도로 유지되어 있는 열욕(熱浴, hot bath)으로 퀜칭하여 과냉 오스테나이트가 베이나이트로 변태완료하기까지 항온유지한 후, 공기중으로 냉각하는 과정을 오스템퍼링(austempering)이라고 한다. 따라서 이 열처리에서는 템퍼링처리를 별도로 할 필요가 없다. 또한 그림에서 보는 바와 같이 베이나이트로 변태하기 전에 강재 중심부와 표면의 온도가 동일해지므로써 강재내에 열구배가 없기 때문에 처리도중에 내부응력을 최소화 할 수 있다. 따라서 이 방법에 의하면 퀜칭변형과 균열을 방지할 수 있게 되고, 또한 이 처리에 의해서 형성된 베이나이트 조직은 퀜칭.템퍼링된 강재의 조직보다 인성이 매우 우수해진다. 일반적으로 오스템퍼링처리가 퀜칭.템퍼링처리보다 인성과 연성을 향상시키는데 크게 기여하는 것을 알 수 있다. 물론 이 강의 P함유량이 비교적 많고(0.044%), 템퍼링온도도 315℃이므로 전술한 템퍼링취성에 의해서 어느정도 인성이 저하되었다는 사실을 간과해서는 안된다.
(3) 마르퀜칭 오스테나이트 상태로부터 Ms 직상의 열욕으로 퀜칭하여 강의 내외가 동일한 온도가 되도록 항온유지한 후, 과냉 오스테나이트가 항온변태를 일으키기 전에 공랭시켜서 마르텐사이트 변태가 천천히 진행되도록 하는 처리방법을 마르퀜칭(marquenching)이라 한다. 마르퀜칭의 경우 강재의 표면과 중심부의 온도는 Ms온도 직상의 유지온도까지는 서로 다른 속도로 냉각되지만 공랭시 마르텐사이트로 변태하는 도중에는 내외부의 온도차이가 없다. 따라서 이 방법에 의하면 수냉한 마르텐사이트보다는 경도가 다소 저하되지만, 변태후 내부응력이 최소화되므로 열처리 균열이나 변형의 가능성이 매우 적다는 것이 큰 장점이다. 이 처리시 Ms점 이하의 열욕을 사용하는 경우나 열욕으로부터 꺼내어 서냉하는 경우에 비교적 높은 온도에서 변태된 마르텐사이트는 부분적으로 템퍼링되어 있지만 대부분의 마르텐사이트는 템퍼링되어 있지 않으므로 이 처리후에는 필히 템퍼링을 실시해야만 한다. 고탄소강, 게이지강, 베어링강 등과 같이 수냉 또는 유냉하면 균열이나 변형을 일으키기 쉬운 강종에 이 방법이 적합하다. 참고문헌 1. G. Krauss and J. F. Libsch : Phase Diagrams in Ceramic, Glass and Metal Technology, A. M. Alper(Ed.), Academic Press, New York, 1970 2. 延倫模, 池武晟, 宋鍵, 洪英煥 : 金屬材料, 機電硏究社, 1994 3. 歌川 寬 : やさしい 金屬熱處理技術の基礎, 啓學出版, 1981 4. G. Krauss : Principles of Heat Treatment of Steels, American Society for Metals, Metals Park, Ohio, 1980 5. 大和久重雄 : 金型の熱處理ノ-ト, 日刊工業新聞社, 1991 6. C. R. Brooks : Heat Treatment of Ferrous Alloys, McGraw-Hill, New York, 1979 7. 日本熱處理技術協會 : 熱處理の基礎(Ⅰ), 日刊工業新聞社, 1970 8. C. R. Barrett, W. D. Nix, and A. S. Tetelman : The Principles of Engineering Materials, Prentice-Hall, New Jersey, 1973 9. L. E. Samuels : Optical Microscopy of Carbon Steels, American Society for Metals, Metals Park, Ohio,1980 10. 金屬熱處理技術便覽編輯委員會 : 金屬熱處理技術便覽, 日刊工業新聞社, 1961 11. P. M. Unterweiser, H. E. Boyer, and J. J. Kubbs : Heat Treater's Guide, American Society for Metals, Metals Park, Ohio, 1982 12. Atlas of Isothermal Transformation and Cooling Transformation Diagrams, American Society for Metals, Metals Park, Ohio, 1977 13. Alloying Elements in Steel, American Society for Metals, Metals Park, Ohio, 1966 14. M. A. Grossman and E. C. Bain : Principles of Heat Treatment, 5th Ed., American Society for Metals, Metals Park, Ohio, 1964 15. B.O.B : Improved Tool Life by The Cryotough Treatment, Metallurgia, Vol. 56, No. 4, 1989 16. R. F. Barron : Cryogenics, Cryo-tech, Heat Treating, 1974, 6 17. C. J. McMahon : Temper Brittleness in Steels, ASTM Special Technical Publication No. 407, 1968, p.127 18. C. J. McMahon et al : Acta Met., 24(1976) 695 19. R. Viswanathan : Met. Trans., 2(1971) 809 20. 大和久重雄 : ハイスの熱處理ノ-ト, 日刊工業新聞社, 1993 21. G. E. Hicho, C. H. Brady, L. C. Smith, and R. J. Fields : J. Heat Treat., 5(1987)7 |
| |